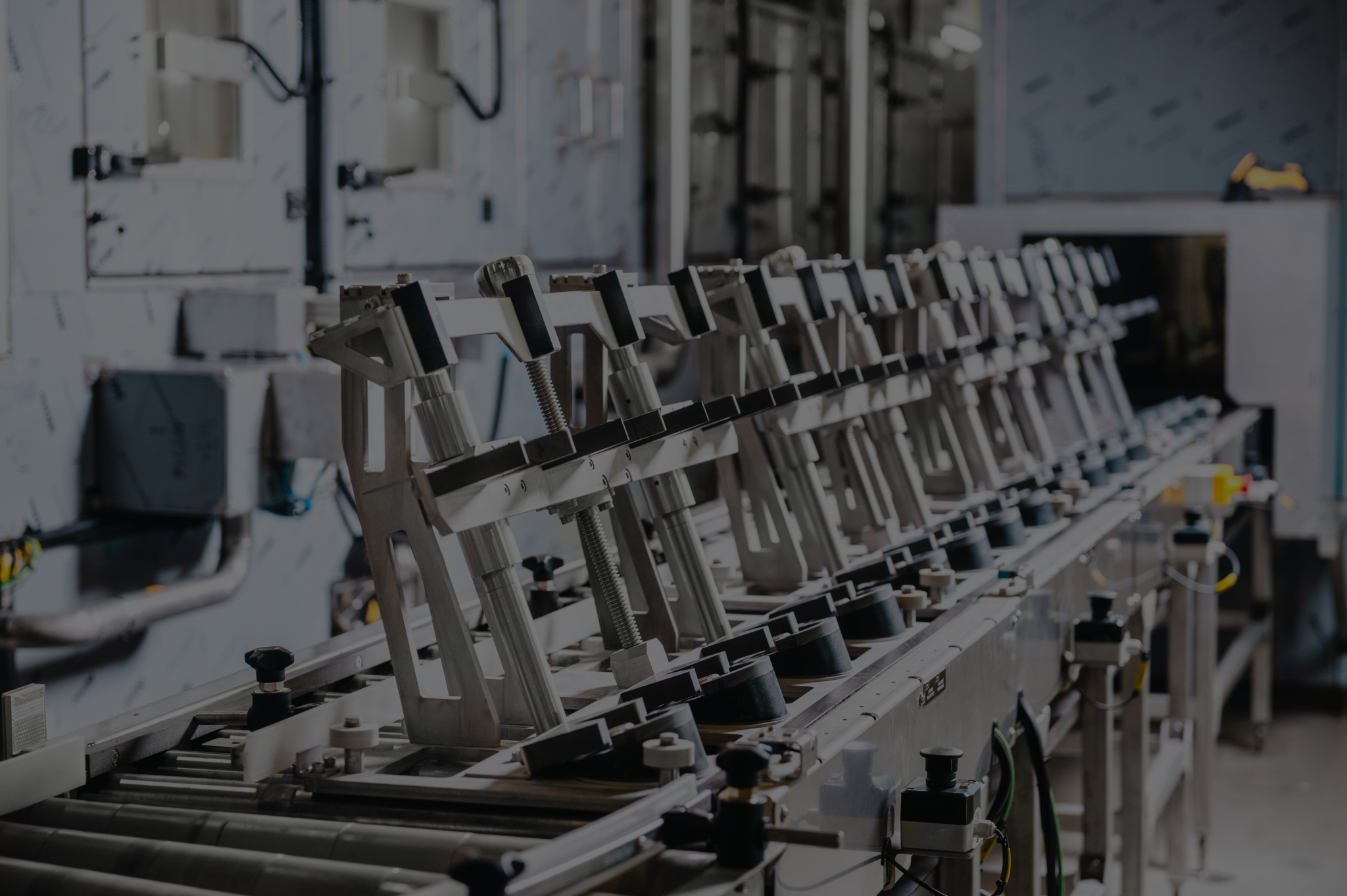
Solution for industrial cleaning of shock absorber cylinder tube
Our client, a global supplier to the automotive industry, approached us for help with the industrial cleaning process of shock absorber cylinder tube. After the KTL painting process, organic contaminants such as oil or emulsion residues and inorganic contaminants (metal shavings, textile fibres) had to be removed from these parts. The clean parts would then go on to the next stage of assembly.
What did the customer require?
- Cleaning of over 40 types of parts with complex shapes and occasionally varied sizes
- Adapting the parts transport through the cleaning process in a way that makes it possible to work with new designs and different types of dampers in the future – flexibility of the solution for a wide range of modifications of part types
- Meeting strict cleanliness standards – maximum particle size below 500 µm
- Ability to reprogram the machine quickly and easily
- Improving ergonomics – loading and unloading – while increasing machine capacity
Solution implemented at the customer’s site
NOYEN’s experts suggested a cleaning process in a NOYEN EXPERT T tunnel type machine. The standard cleaning machine manufactured by the company for more than a dozen years has been specifically designed to meet the customer’s requirements. The project involved a full line concept, in which the cleaning process starts with manual loading of the dampers onto the transport pallets by the operator. The machine features an innovative concept of arranging the parts on the carrier (pallet), inclined at a specific angle, which enables ergonomic work of the operator who loads and unloads the parts, as well as allows automatic changeover of the pallets for the given type of reference and quick automatic adjustment the machine for different parts. In this concept (which is also a foolproof concept), the item does not have to be positioned accurately on the pallet, which is an additional convenience for the operator and a factor contributing to reduced loading times.
The parts are then subjected to a medium- and high-pressure washing process at 42 bar with dedicated retractable spray manifolds, which effectively remove dirt from hard-to-reach areas such as the inside of the damper. The next sections are medium-pressure rinsing >5 bar and hot-air drying with blow-off collectors and air knives sourced by side-channel blowers. The last part of the process is to stabilise the temperature of the part to the level required by the customer – <43°C, so that the operator does not have to wear heat-resistant gloves.
All processes take place simultaneously, and the parts are transported in batches of 4, which has a significant impact on process efficiency.
What did the client gain by working with NOYEN?
- Use of automatically converting and adjusting carriers (pallets) – > for each barcode a proper transport pallet for the given type of part is assigned, along with a dedicated cleaning program
- A dedicated cleaning program that optimises efficiency, as some references are washed, rinsed and dried in a standard cycle time and others in a shortened one. By identifying and tracking parts and pallets, the cleaning machine automatically activates the dedicated programme in the given section.
- High efficiency = washing times of 5s / 1 part, 20s / pallet (4 parts per pallet) per cycle
- Achieving the technical cleanliness standards required by the client
- Handling an extremely different shape parts in one machine
- Loading repeatability and stability of the process
- An application which is not only an industrial cleaning machine, but also a transport line, with automated high performance systems, taking into account the ergonomics of the operator stations
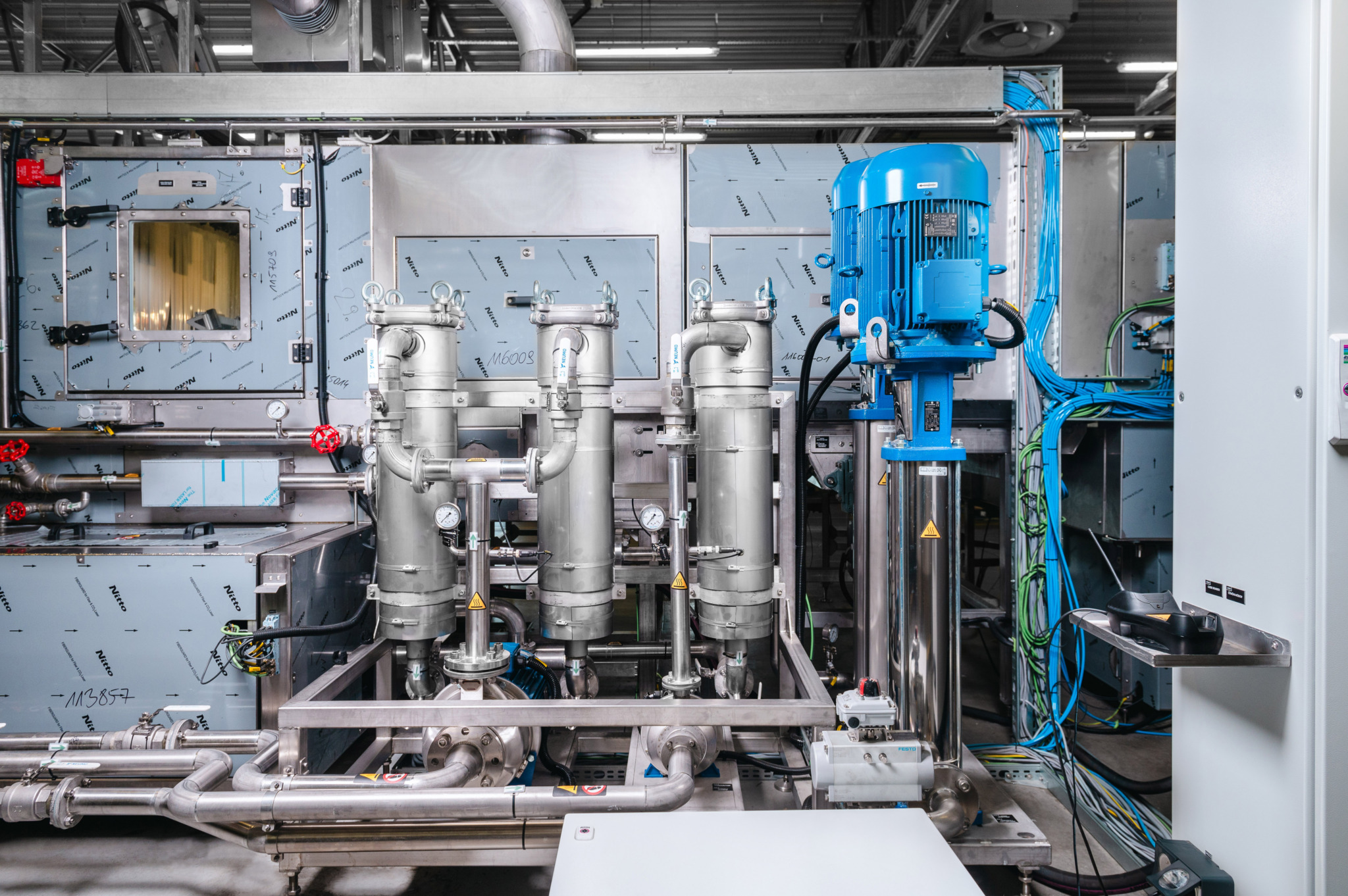
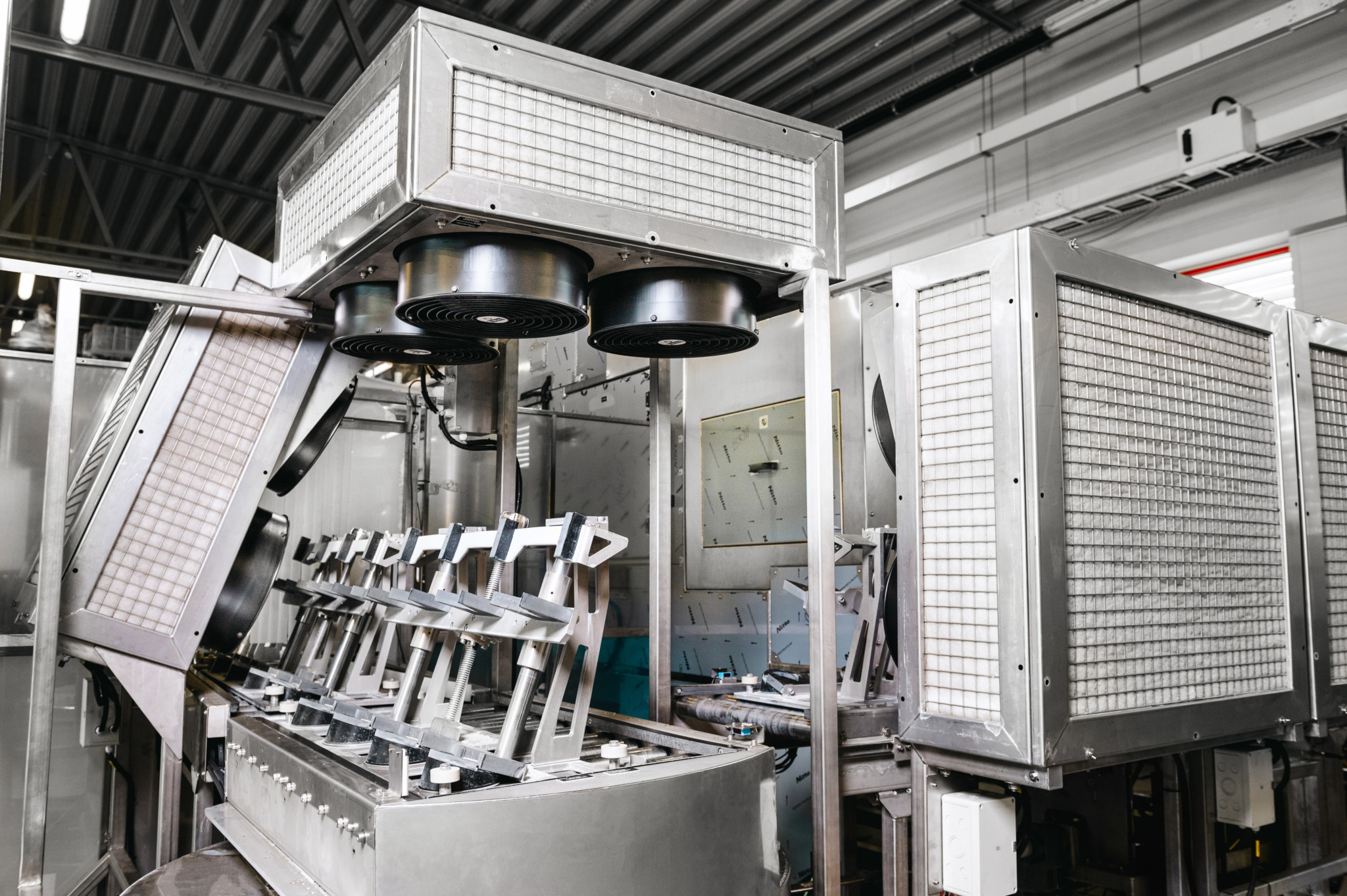
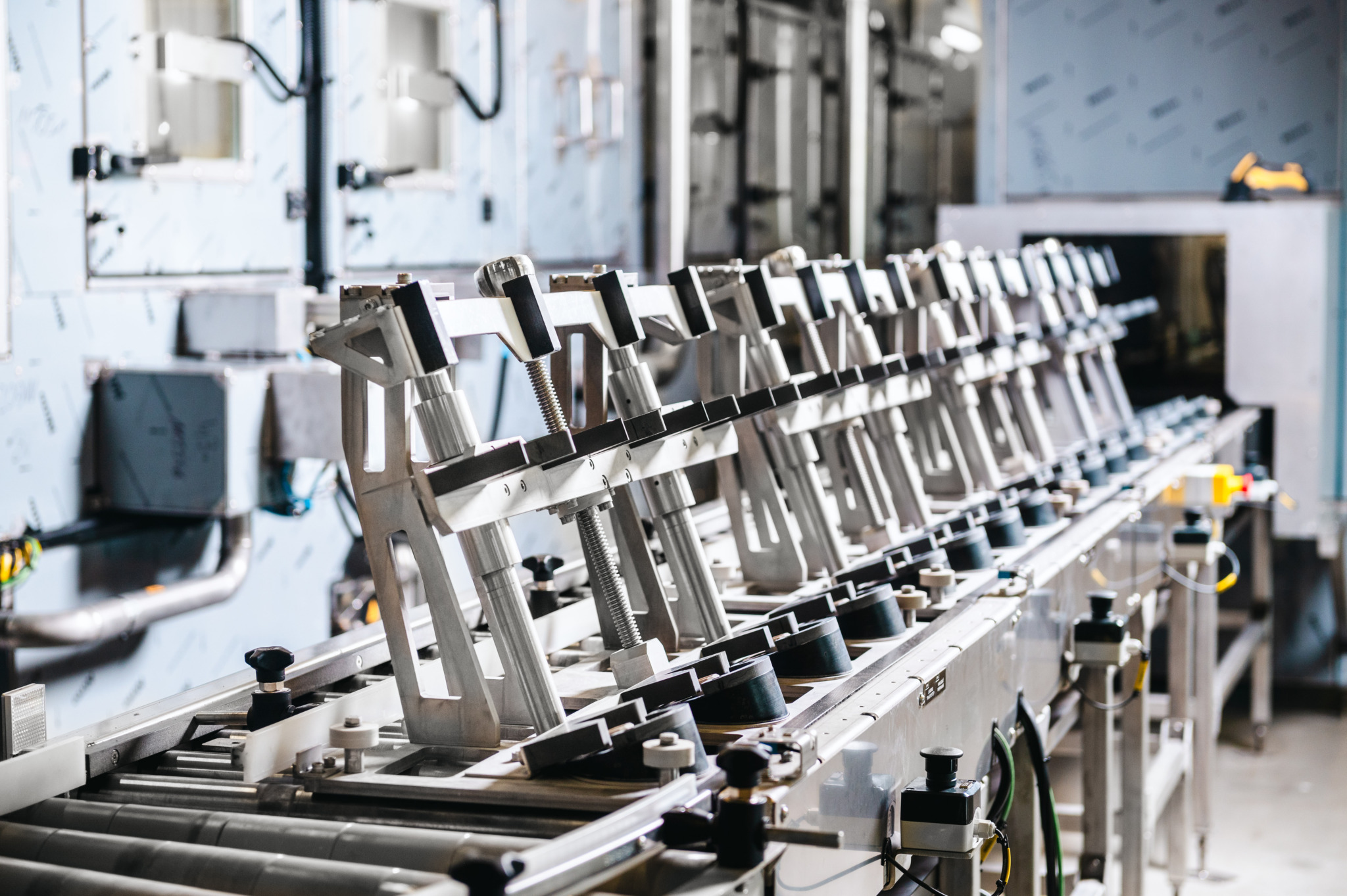
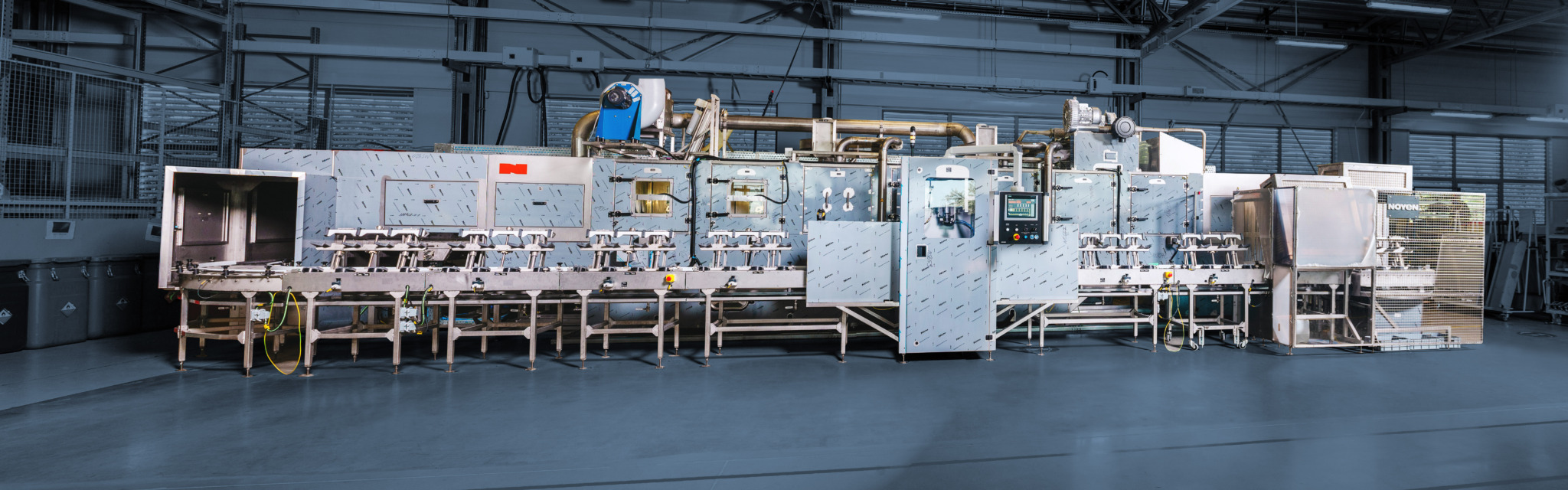
Nothing is impossible
It will be much easier if you tell us what is the matter. Save some time and sign up for a free consultation. Our expert will advise you free of charge.