The importance of quality control of the cleaning process and the possibility of constant verification of the technical condition of the cleaning machine is known to those companies in which the components cleaning is an important element of the production process. Until now, solutions for liquid sampling systems and device self-diagnostics have rarely been offered on the domestic market. Taking into account the fact that companies from the automotive, machinery, aviation and medical industries are interested in the possibilities of automated liquid sampling as well as ongoing monitoring of process parameters of cleaning machines, NOYEN meets the needs of the market by implementing new functionalities.
The implementation of modern functionalities became possible thanks to the company’s own R+D work, while the funds for the implementation of the project were obtained from the Operational Programme Eastern Poland 2014-2020. The project is in line with the policy of continuous innovation of applied technologies and technical solutions, consistently implemented by NOYEN for many years.
Automated liquid sampling system – why is it important?
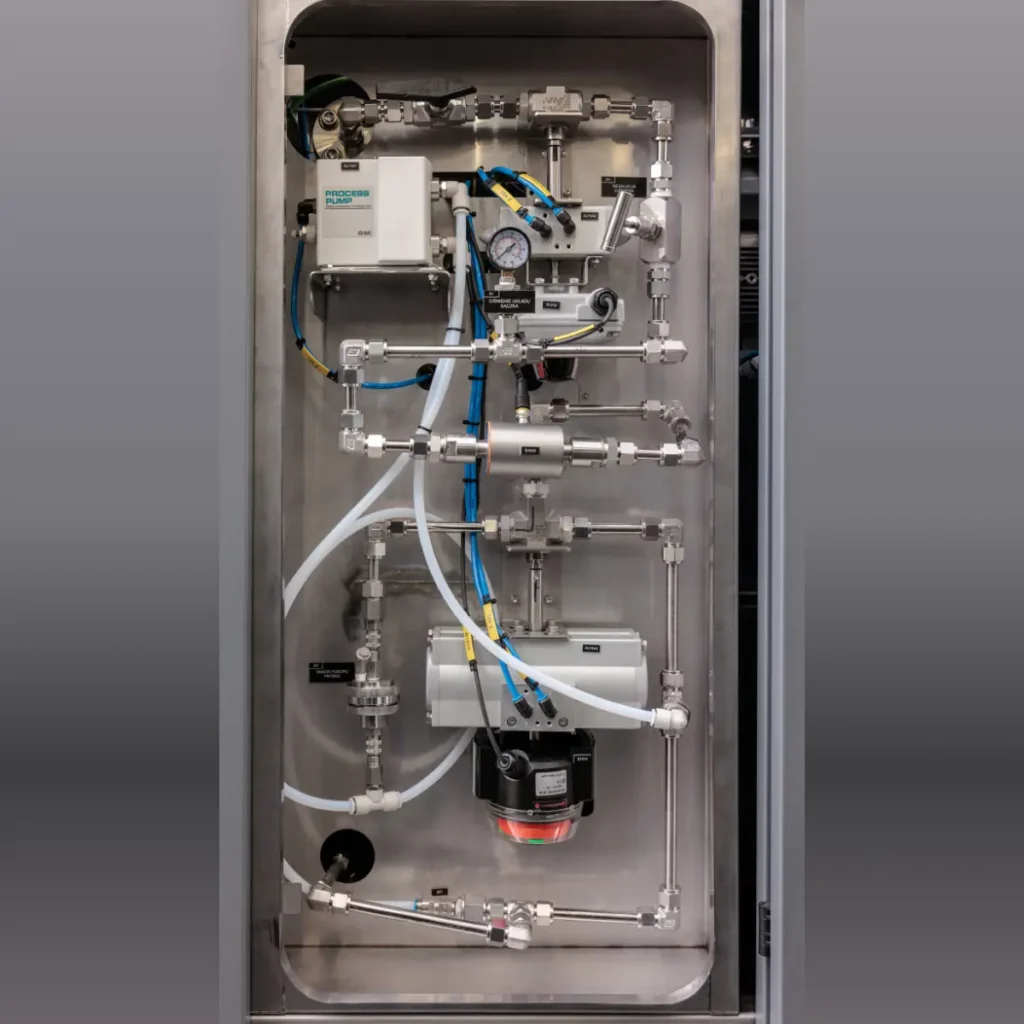
The basis of the cleaning process’ control, in order to ensure the cleanliness of components in a stable and efficient manner, is quality control with targeted process engineering measures as well as measurement, testing and inspection technology. This inspection involves taking samples of liquids from the cleaning medium in order to assess its condition. NOYEN’s automatic bath impurity sampling system offers a reproducible and accurate procedure for extracting contaminants from the bath sample onto the laboratory filter, improving the ad hoc quality control of the cleaning process. The use of the system allows to reduce the number of laboratory activities, and thus also to reduce the risk of secondary contaminants appearing on the filter. The volume of the liquid sample to be tested, as well as the flushing volume of the system prior to extraction, are subject to modification by the user, making the application of the system flexible.
The procedure for sampling liquids in most devices on the market is done manually. This results in additional hazards for the laboratory technician, e.g. burns with the working liquid or spillage of the bath on the surface, causing a risk of slipping. Numerous personal protective equipment is therefore required. Thanks to the automatic sampling system used for contaminants from liquids, the sample is taken maintenance-free, which eliminates the risks associated with direct contact with the working medium. An additional advantage of the system is that the amount of liquid used for extraction and flushing of the system is precisely measured by the flowmeter system – this significantly increases the repeatability of results.
Greater control over technical cleanliness
The development of an automatic system for sampling bath contaminants allows to increase control over technical cleanliness without the need to spend a lot of money on it. Greater control over technical cleanliness means an improvement in the quality of products and an increase in the level of technical culture. By controlling the level of liquid contamination, it is possible to optimize the frequency of bath changes in cleaning equipment, which will lead to a reduction in the number of bath changes. This allows to reduce the amount of waste generated by cleaning equipment (up to 750l per year), thus increasing their environmental friendliness.
See how works NOYEN iCleaning – click to watch
Regular self-diagnostics of cleaning machines – a necessary preventive measure
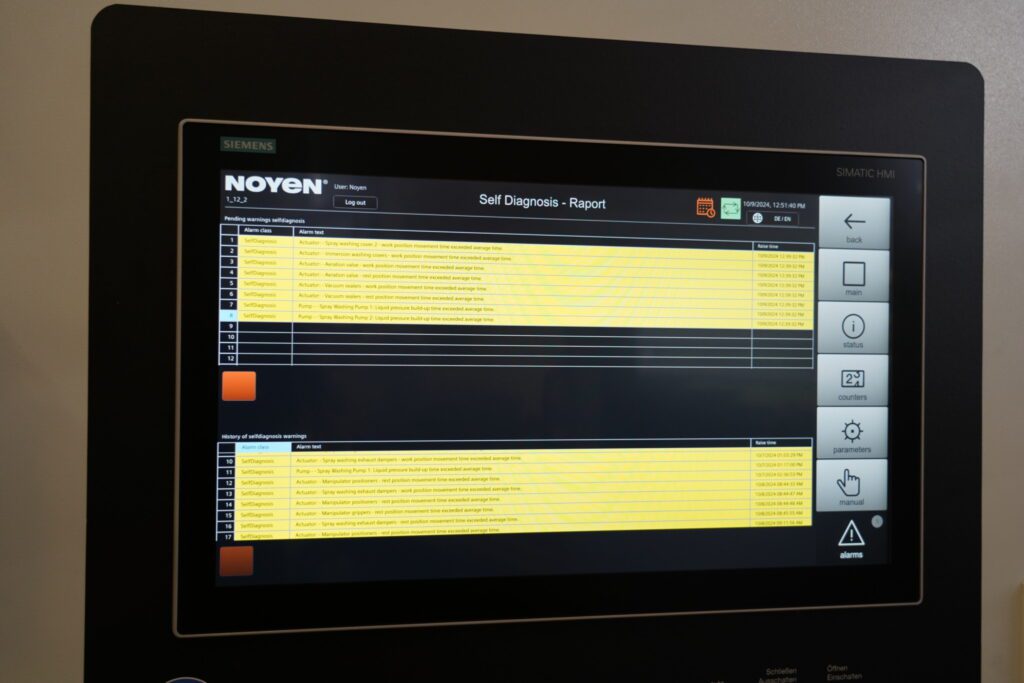
Most of the available on the market cleaning equipment offers the possibility of real-time monitoring of the machine’s process parameters, which is a diagnostic tool in itself. However, this is only symptomatic diagnostics, based on the assumption that if the machine reaches the set parameter values, its functioning is completely correct. This can be compared to the operation of alarm systems. Although they usually provide information about the possible causes of abnormal conditions, they do not provide comprehensive information about the condition of machine components.
The use of the self-diagnostic procedure in NOYEN cleaning devices allows to prevent the occurrence of machine dysfunctions through regular and detailed inspections of the condition of its executive and signalling components. As a result, the user has up-to-date information on the technical condition of the device, on the basis of which he can predict and plan the replacement of key components, reducing the time of possible production downtime to an absolute minimum. Prevention in this case gives a greater guarantee of the continuity of the production process. In addition, diagnostics can be carried out by people with less experience with automation systems.
Significant extension of the life cycle of the cleaning machine
Compared to other machines (not equipped with this feature), a significant increase in the life cycle of the machine can be observed. Self-diagnostics allows you to pinpoint a single component that is worn or damaged, without the need to replace whole, often expensive components. The function also allows you to predict the failure of a given element – the so-called “predictive maintenance” – by measuring operating parameters. This allows the user to prevent failure by taking appropriate action.
The solutions proposed by NOYEN will be used by all customers who care about maintaining the high quality of their products. Continuous process control is the key to maintaining high and repeatable final quality.
NOYEN – a manufacturer of industrial cleaning machines offering comprehensive products and services regarding industrial cleaning, industrial cleaning service, automation, lab testing and chemicals. Have a look at our wide variety of cleaning machines and find out how NOYEN can support you – contact our specialists.
Nothing is impossible
It will be much easier if you tell us what is the matter. Save some time and sign up for a free consultation. Our expert will advise you free of charge.