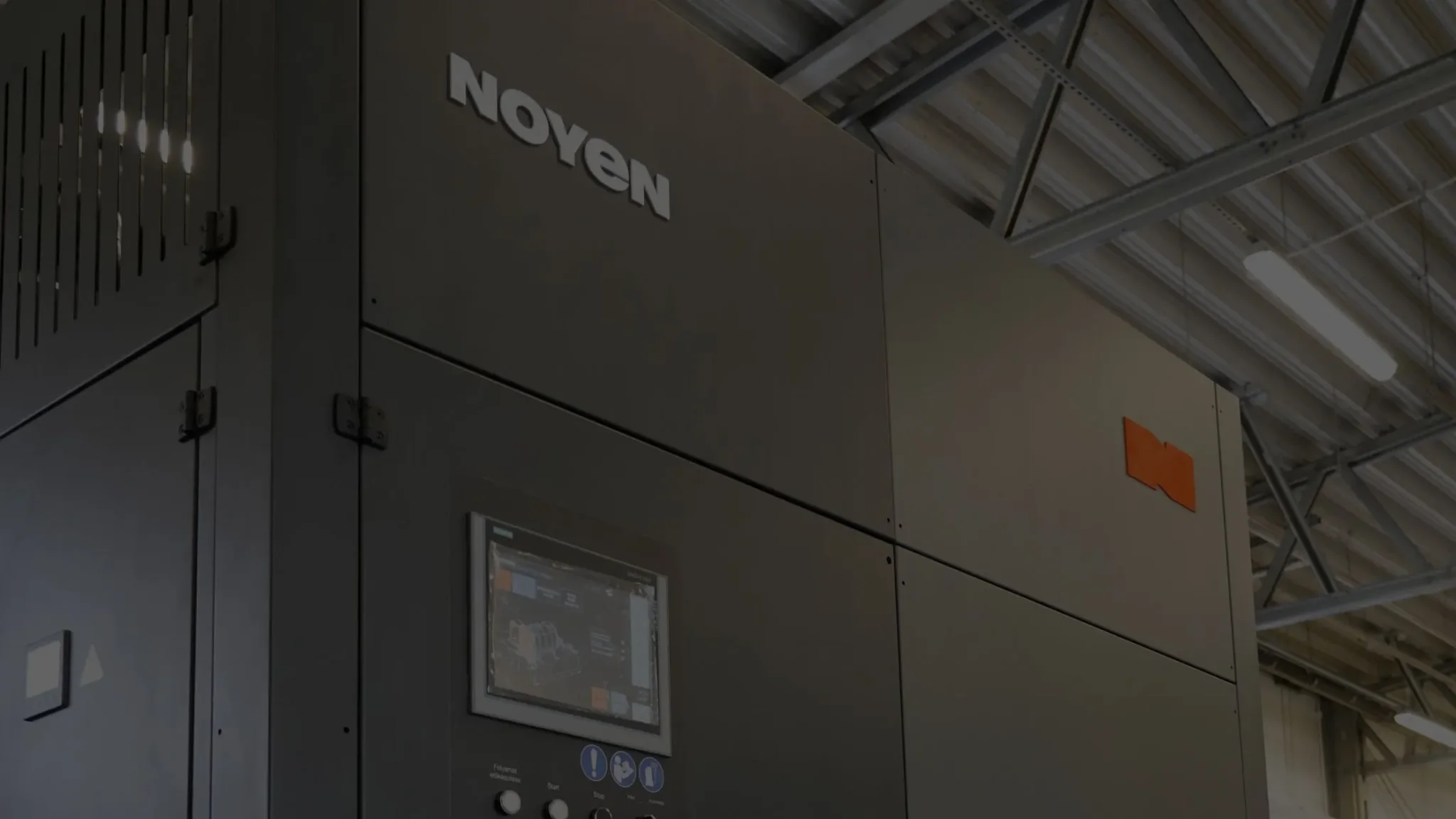
Industrial cleaning of hydraulic systems
Our client is one of Hungary’s market leaders in the field of metalworking and production of parts for the automotive and railroad industries – supplier to multinationals.
What did the client require?
The customer approached us with the challenge of removing contaminants such as chips, coolant and residual contaminants from hydraulic systems made of cast iron after the machining process. The technical cleanliness required was at the level of the target customer’s standards, i.e., an Original Equipment Manufacturer (OEM) company, where industrial cleaning must be done according to strict standards defined by the Component Cleanliness Code (CCC), which we can summarize as level requirements:
- Particle range in µm: 100-400 Permissible particles: 1000-2000
- Particle range in µm: 400-600 Acceptable number of particles: 16-32
- Particle range in µm: 600-1000 Permissible number of particles: 0
Based on our experience and knowledge at NOYEN, we easily took on the challenge of cleaning under the cleanliness standards specified by the customer.
Solution implemented at the client’s site
The solution offered consists of washing and degreasing workpieces in a NOYEN Compact 400 machine.
To ensure the best results, the process is carried out using water-based detergents and is based on a spray method using a nozzle system and immersion washing assisted by rotating the basket around its longer side. Parts are cleaned from all sides due to complete immersion in the chamber.
The process consists of several stages: washing, rinsing, hot air drying, vacuum drying. The device allows the use of as many as 3 technologies for washing workpieces: spray, immersion and ultrasonic. The washing cycle time is about 9 min 50 s.
The device is equipped with double filtration, which allows filter cartridges to be changed without stopping the machine, improving the OEE score.
The NOYEN Compact 400 proposed by NOYEN effectively removes contaminants of various origins and intensities. The use of a servo drive gives the possibility to set the basket in any position and control the position of the parts during the process. This makes it possible to thoroughly wash parts with complex geometries. Vacuum drying makes it possible to lower the temperature of the parts after the washing process, which facilitates their faster preparation for subsequent production stages.
The most important solution implemented in the NC400 is an enlarged process chamber, allowing parts to be washed simultaneously in two baskets. This makes it possible to wash 4 parts at the same time, instead of 2. The NC400 machine meets the cleanliness requirements expected by the customer, and also allows to increase the washing capacity in one cycle – practically twice. The use of this solution was the most important added value, as it fit perfectly into the customer’s current needs.
The machine gives the customer the opportunity to have almost twice the capacity at a price not much higher than a machine equipped with a single basket, while maintaining compact dimensions. The NOYEN Compact 400 machine is also prepared for possible future automation.
Cleaning quality meets stringent technical cleanliness standards confirmed by tests in accordance with ISO 16232 and VDA 19.1 thanks to features such as full part rotation and multi-level filtration. The high quality of the process is also guaranteed by the cylindrical shape of the chamber and ultrasonic transducers in the form of rods for better chamber cleanliness and optimal ultrasonic distribution in the chamber.
Dimensions of NOYEN Compact 400: 3750 x 2450 x 2960 mm
Dimensions of process baskets: 650 x 470 x 400 mm
What did the client gain by working with NOYEN?
- Nearly doubled productivity in a single cycle
- Increased level of technical availability of the machine, which has a positive impact on maintenance
- High cleaning quality in accordance with established technical cleanliness standards
- Process stability
- Comprehensive cooperation and individual approach at each stage of machine development
- The possibility of faster preparation of workpieces for further stages of production thanks to the use of effective vacuum drying
If you need industrial cleaning and count on a proven business partner with many years of experience, contact us.
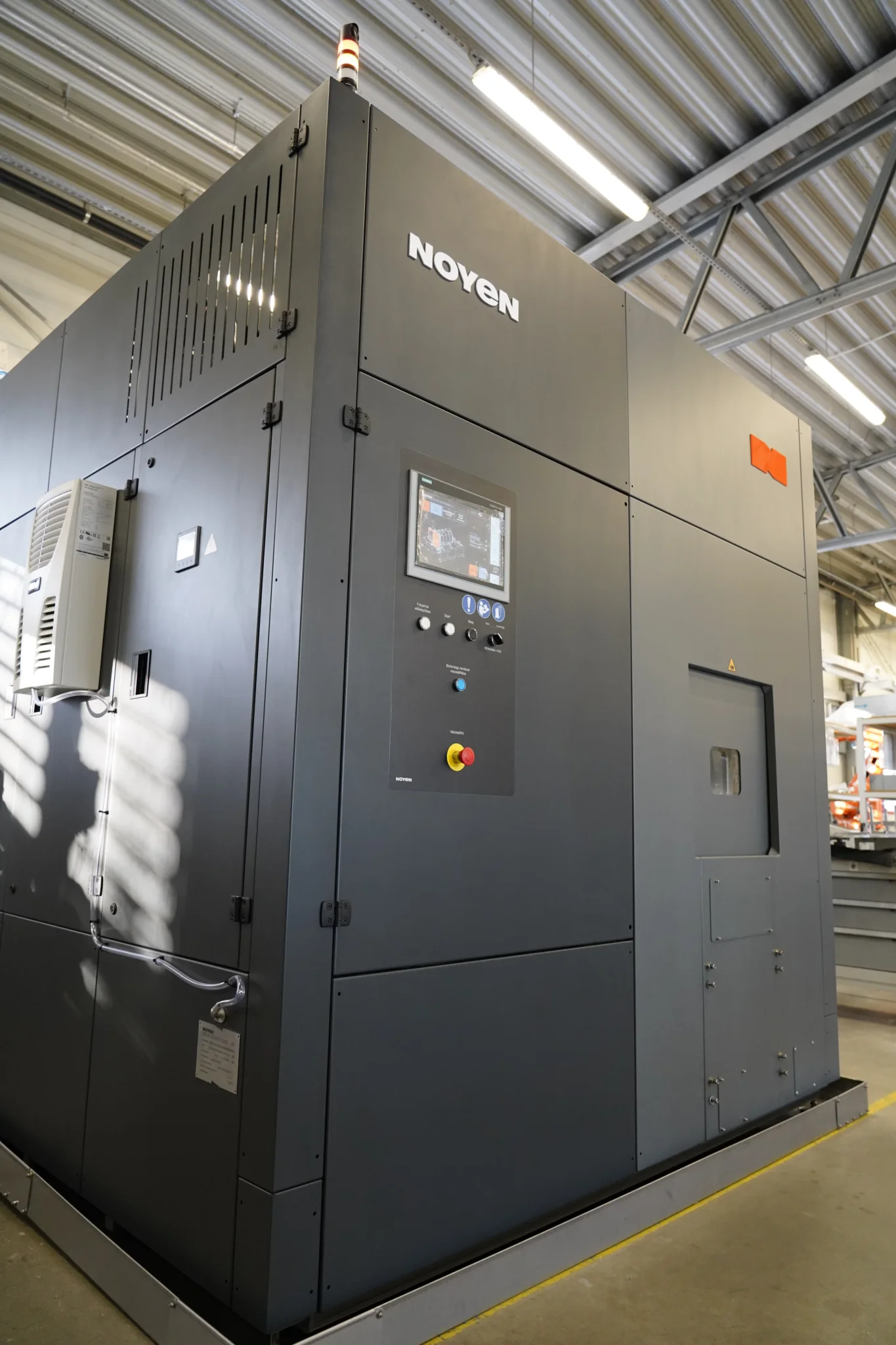
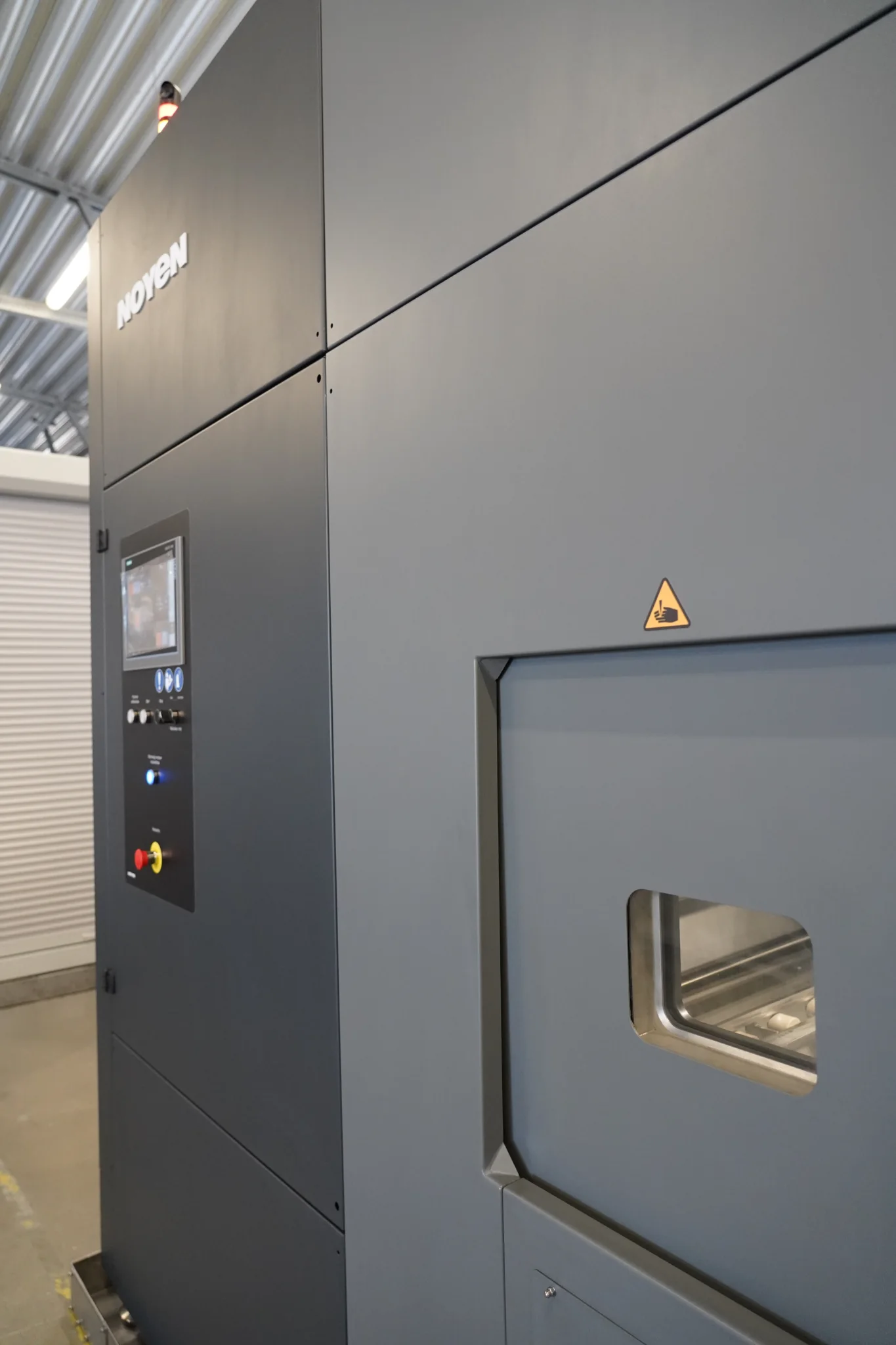
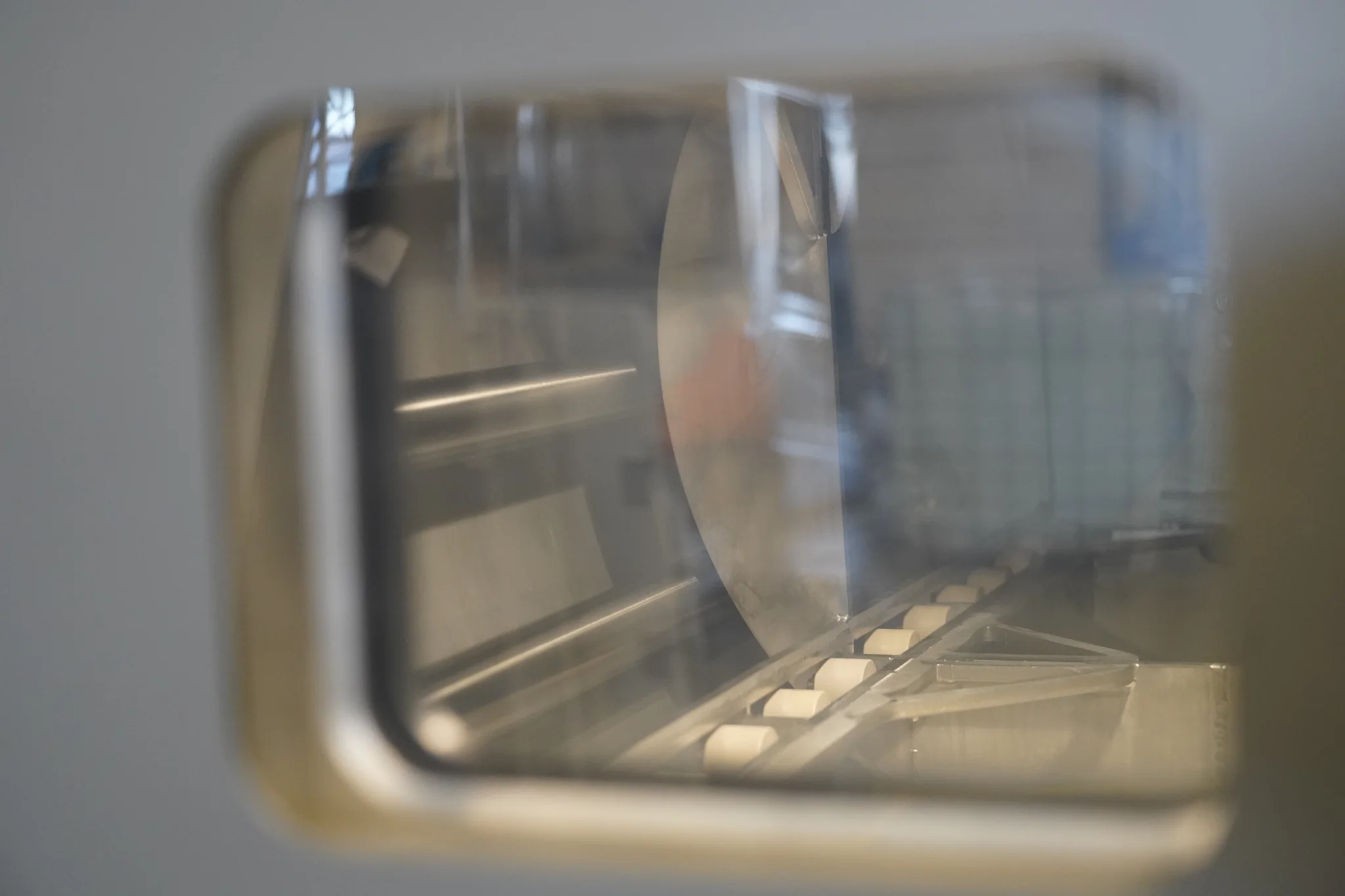
Nothing is impossible
It will be much easier if you tell us what is the matter. Save some time and sign up for a free consultation. Our expert will advise you free of charge.