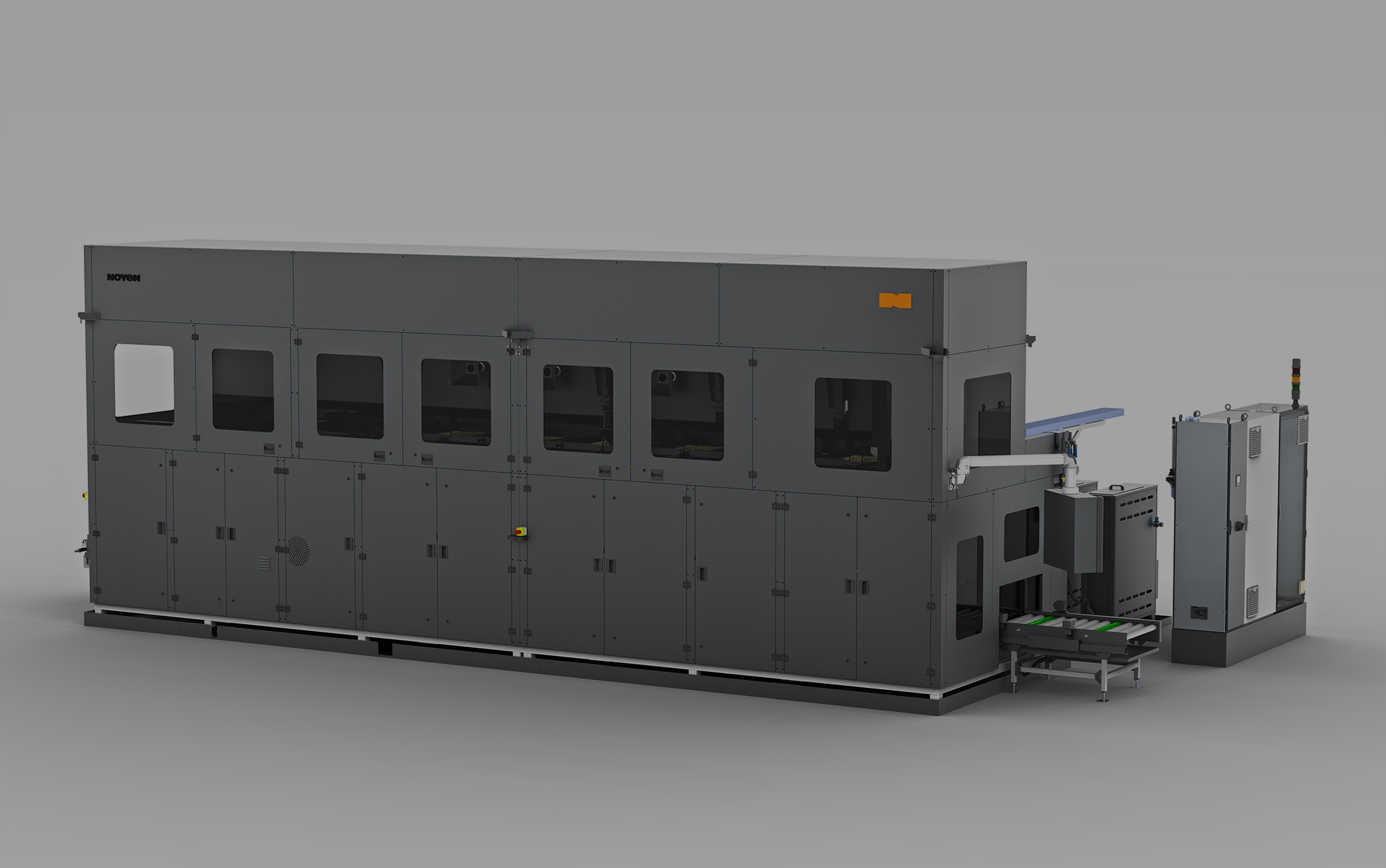
Cleaning of hydraulic fittings using ultrasonic and spray methods
What did the customer require?
The plant produces hydraulic fittings in carbon and stainless steel, as well as copper and CuNiFe. After the machining process, these parts were contaminated with chips and machining fluids. All contamination had to be removed, while protecting the surface of the parts from corrosion. For this reason, the customer turned to NOYEN.
Specific project requirements:
Cleanliness requirements:
- parts degreased, clean, dry, without chips wettability ≥ 40mN
- Selection of technology and products for degreasing
- Corrosion protection for the duration of storage
It is important to be well-prepared for any project – which is why NOYEN’s work began with laboratory tests. The tests conducted in NOYEN’s specialised laboratory made it possible to determine which cleaning parameters and products should be used in order to effectively degrease the workpieces, remove contaminants, achieve a wettability of ≥ 40mN, and protect the product from corrosion during storage.
The solution implemented at the customer’s site
The washing and degreasing process is performed using aqueous cleaning agents. As the workpieces are made of different types of metal, washing must also involve different chemical products. For washing of the steel parts, a 4% solution of NOYEN SG was used – it is a high-alkaline product with strong degreasing properties. Rinsing of these parts is carried out with NOYEN MI – an alkaline formulation designed to protect cast iron and ferroius metals against corrosion – with the addition of demineralized water. Parts made of copper and CuNiFe are washed with a 6% solution of NOYEN KG15, which is based on glycolic acid. This product efficiently cleans and removes oxides of copper, aluminium, zinc and iron. Thanks to the tests carried out beforehand, the NOYEN team was confident that these formulations would do best to clean and protect the parts.
For the best results in the cleaning of fittings, NOYEN recommended a machine from the EXPERT T line. The machine is outfitted with up to 7 process chambers, making it possible to wash, rinse and dry parts made of 4 different materials at the same time. Thanks to the use of a transport manipulator and an automatic chemical dosing system, the time required to operate the machine is significantly decreased. The machine has 2 filter housings which work alternately, which means that the filters can be replaced without interrupting the work process. The efficiency of the washing process is guaranteed by the 360° rotation of the basket in each tank, as well as the positioning of the spray nozzles on 4 sides of the basket, which allows the washing solution to reach every nook and cranny of the cleaned part. The process is as highly efficient – 15 minutes/basket with a maximum load of 50 kg. The optimum size of the chambers, the thermal insulation and the equipment with precision filters allow the machine to save media and cleaning products. The machine communicates with the operator via an intuitive panel.
What did the customer gain by working with NOYEN?
- An individually tailored, comprehensive cleaning system comprising both the cleaning machine and chemicals
- High cleaning quality in accordance with technical cleanliness standards – wettability of ≥40mN
- Time-saving and easy operation of the device thanks to the ability to conduct processes in several chambers simultaneously, as well as automation and the use of intuitive software
- Stability and expected process efficiency – 15 minutes/basket with a maximum load of 50 kg
- Savings in media and cleaning agents thanks to an automatic dosing system, thermal insulation and effective filtration
- Detailed attention to every stage of the process, with efficiency confirmed by lab tests
- Predictable, repeatable cleaning results
- Comprehensive cooperation and individual approach
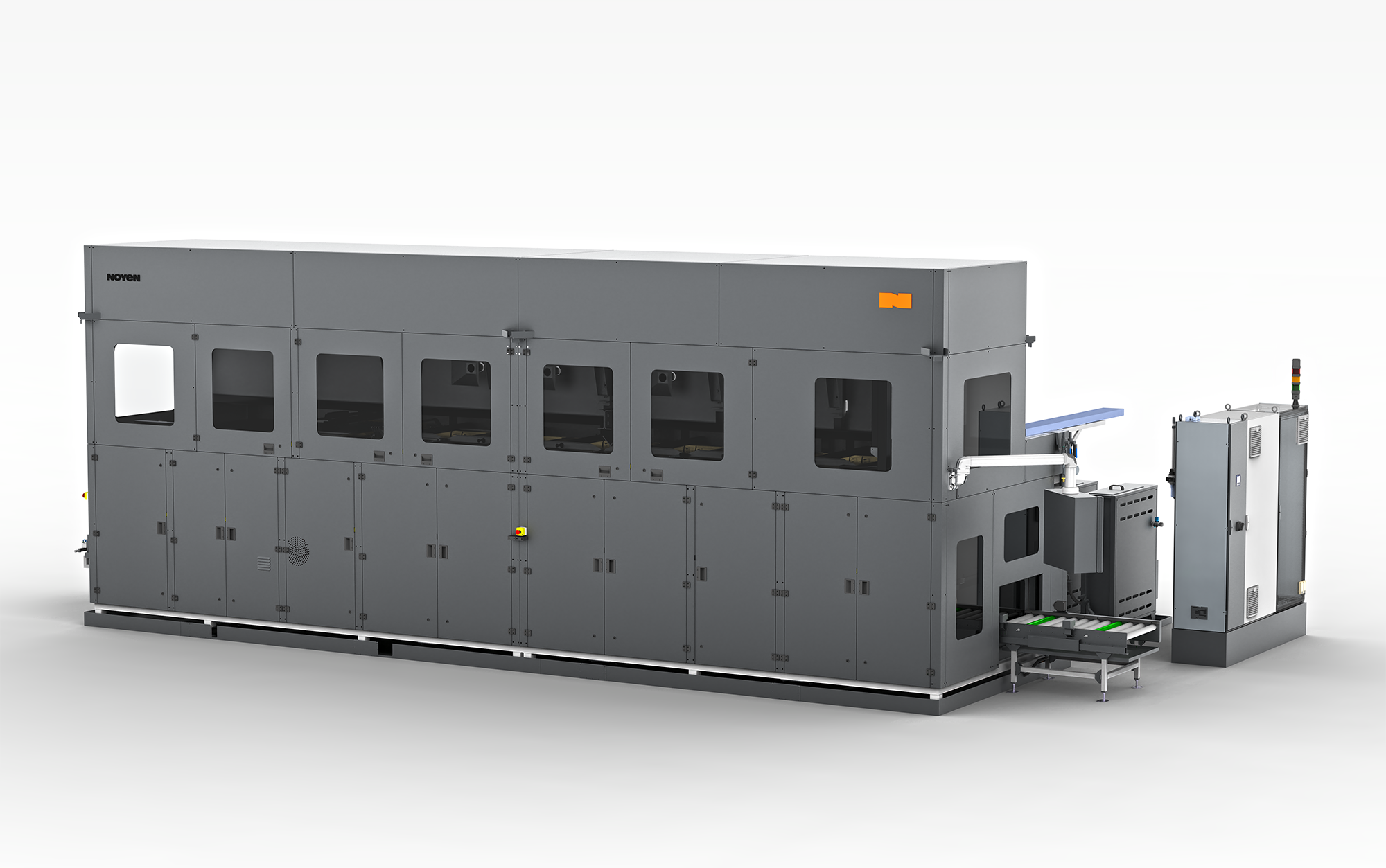
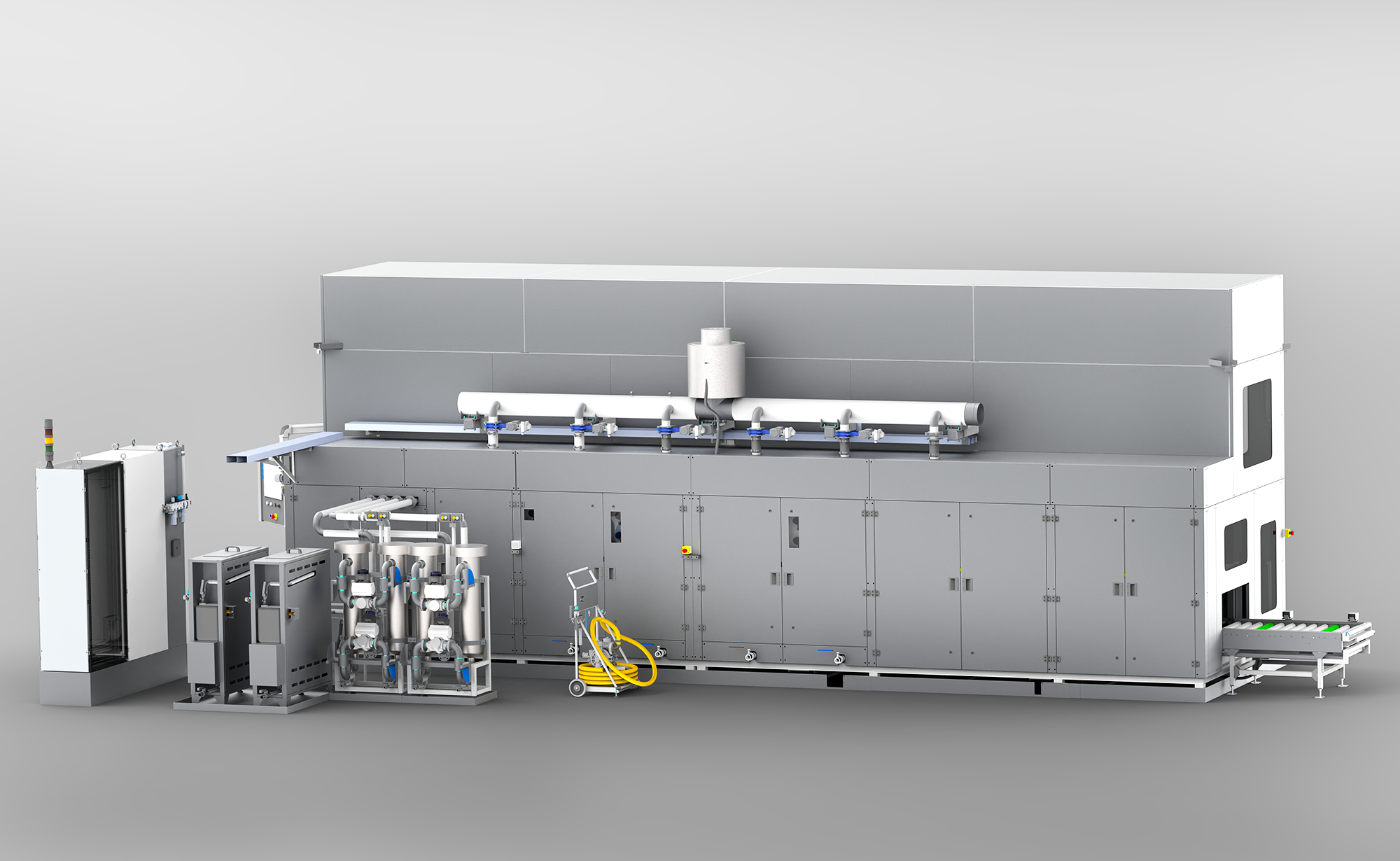
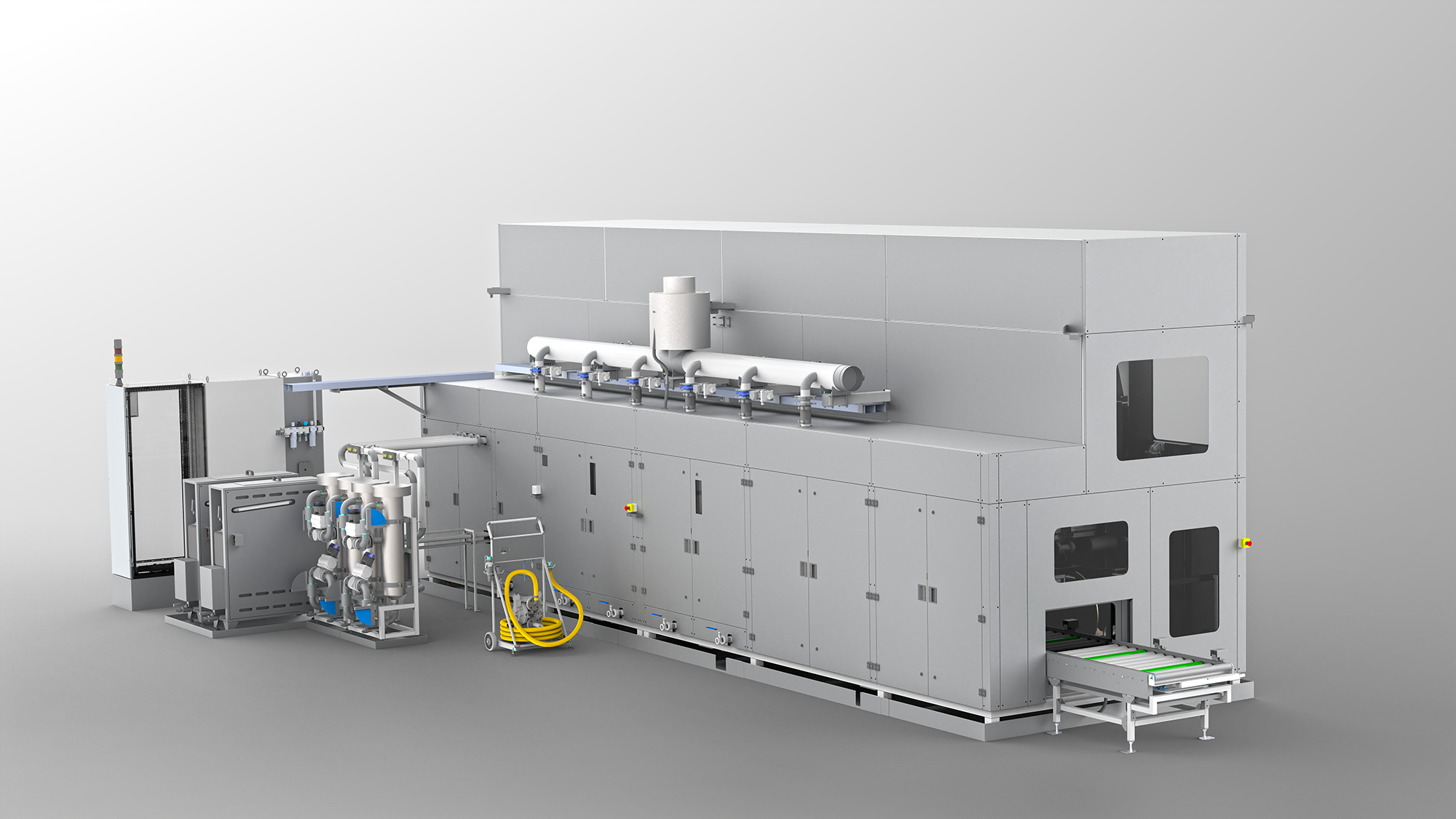
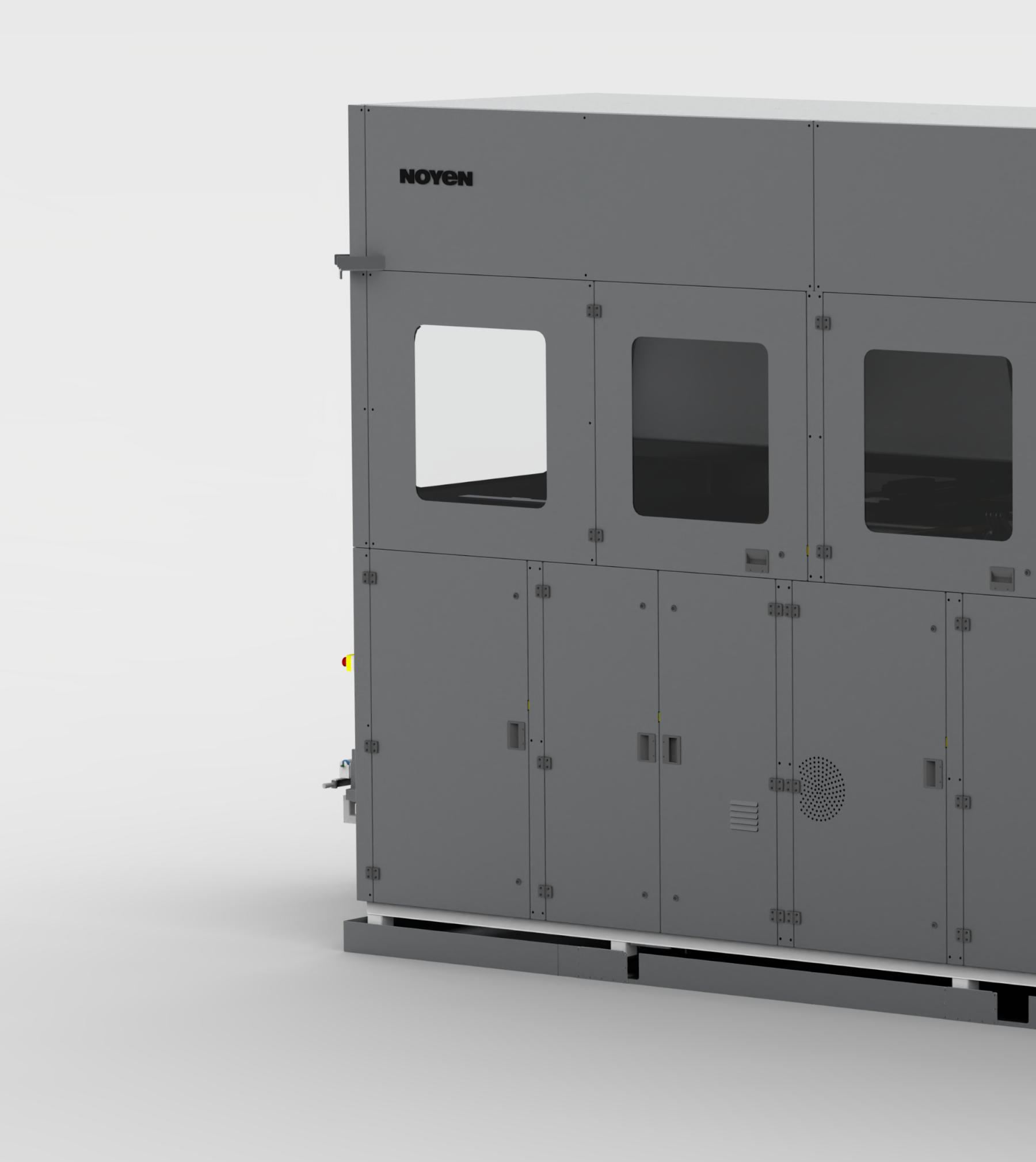
Nothing is impossible
It will be much easier if you tell us what is the matter. Save some time and sign up for a free consultation. Our expert will advise you free of charge.