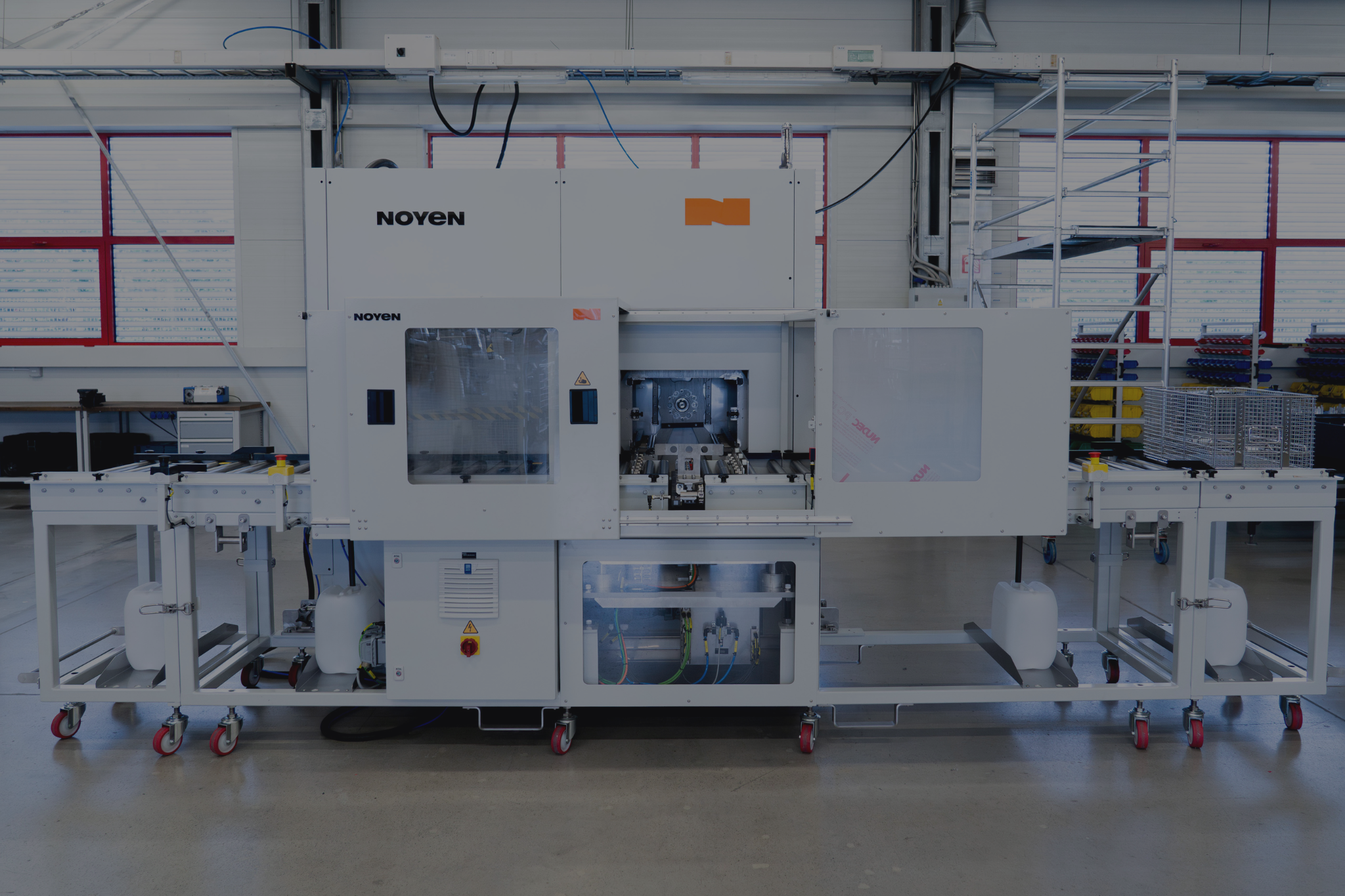
The client from the aerospace industry, that has been working with our team for years already owns nearly 30 of our devices. The new project concerned the implementation of a washing machine for the production process of aerospace engine components. The client needed precise and efficient cleaning of blades and other aircraft engine components prior to assembly, according to its own quality requirements and cleanliness standards.
Solution implemented at the customer’s site
We implemented the NOYEN Compact 200 washing machine. The three-chamber system (one 500-litre wash tub and two 250-litre rinse tubs each) allows customised cleaning programmes for different components.
- Machine dimensions (mm): 2000 (L) x 2200 (W) x 2322 (H)
- Dimensions of work basket (mm): 600 (L) x 400 (W) x 300 (H)
- Loading: 100 kg
- Cycle time: freely programmable
The process consists of several stages: cleaning, first rinse, second rinse and drying. The machine uses two washing technologies: spray and immersion. The use of a servo drive allows controlling the position of the workpiece during the process and placing the basket in any position. With the option to tilt or fully rotate the basket with the workpieces in the immersion, the customer has gained accurately cleaned parts with complex geometries. In addition, the machine is equipped with an automatic loading function and a basket lid recognition system, which minimises the risk of component damage.
The device has a module for automatic measurement of the conductivity in the wash tubs, which enables monitoring the concentration of the cleaning chemistry and ensures a highly efficient cleaning process. All processes are controlled by a modern PLC. The operator panel allows full visualisation of the process and enables control of process parameters such as bath temperature, cleaning, rinsing and drying times.
The washing machine has a self-diagnostic function, which allows it to check its current technical condition. The customer has minimised the risk of unexpected downtime by replacing worn parts in good time. The customer has gain the option to tailor washing programmes to different components, ensuring complete flexibility and optimisation of the process. The machine was also made in a custom colour to fully meet the customer’s aesthetic requirements.
What has the client gained from working with NOYEN?
- Compact cleaning machine adapted to the layout and colours of the production hall
- Safe and precise washing of workpieces with difficult geometries and high material value
- Optimisation thanks to the possibility of realising different processes in one machine
- NOYEN’s full support in the process
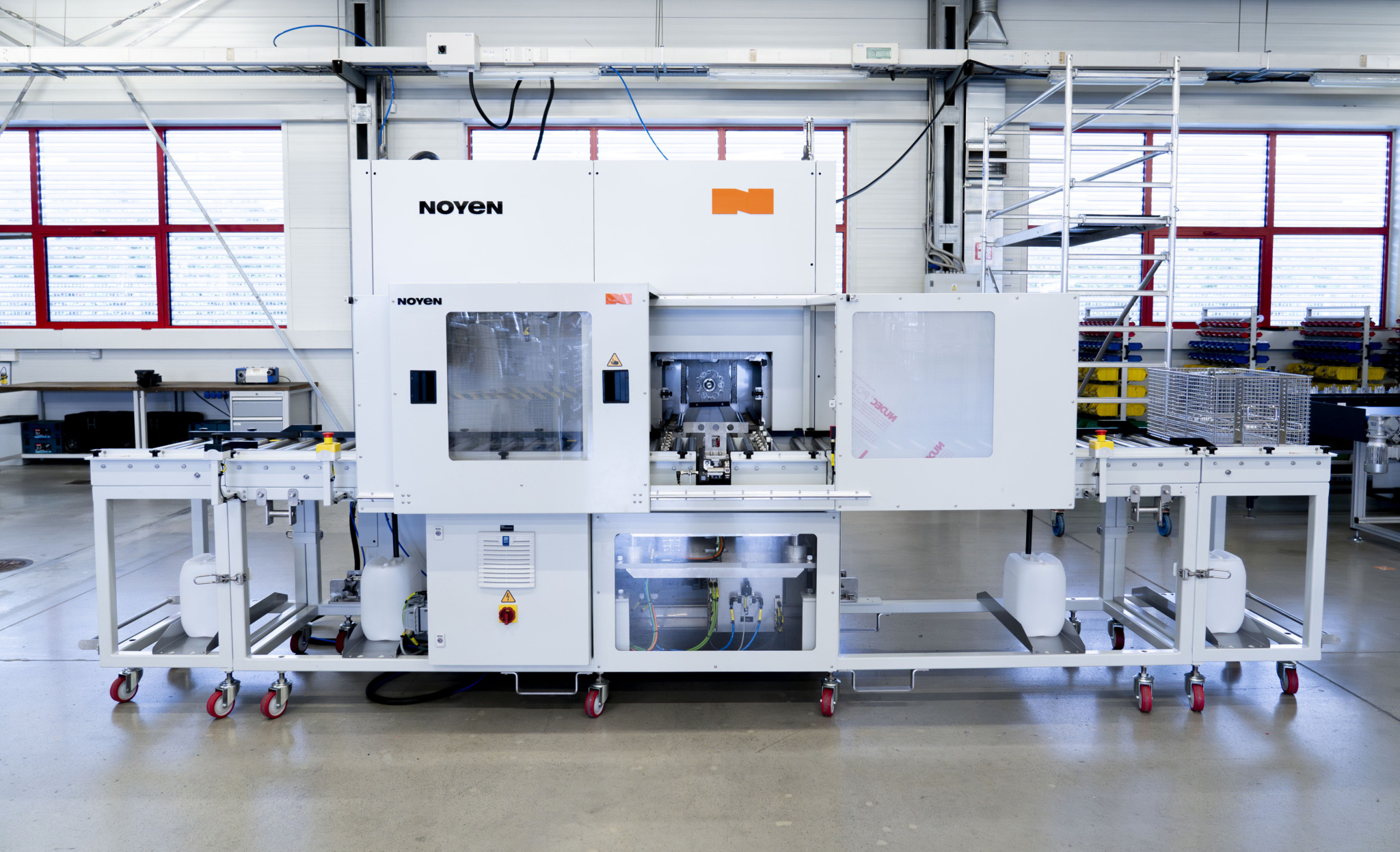
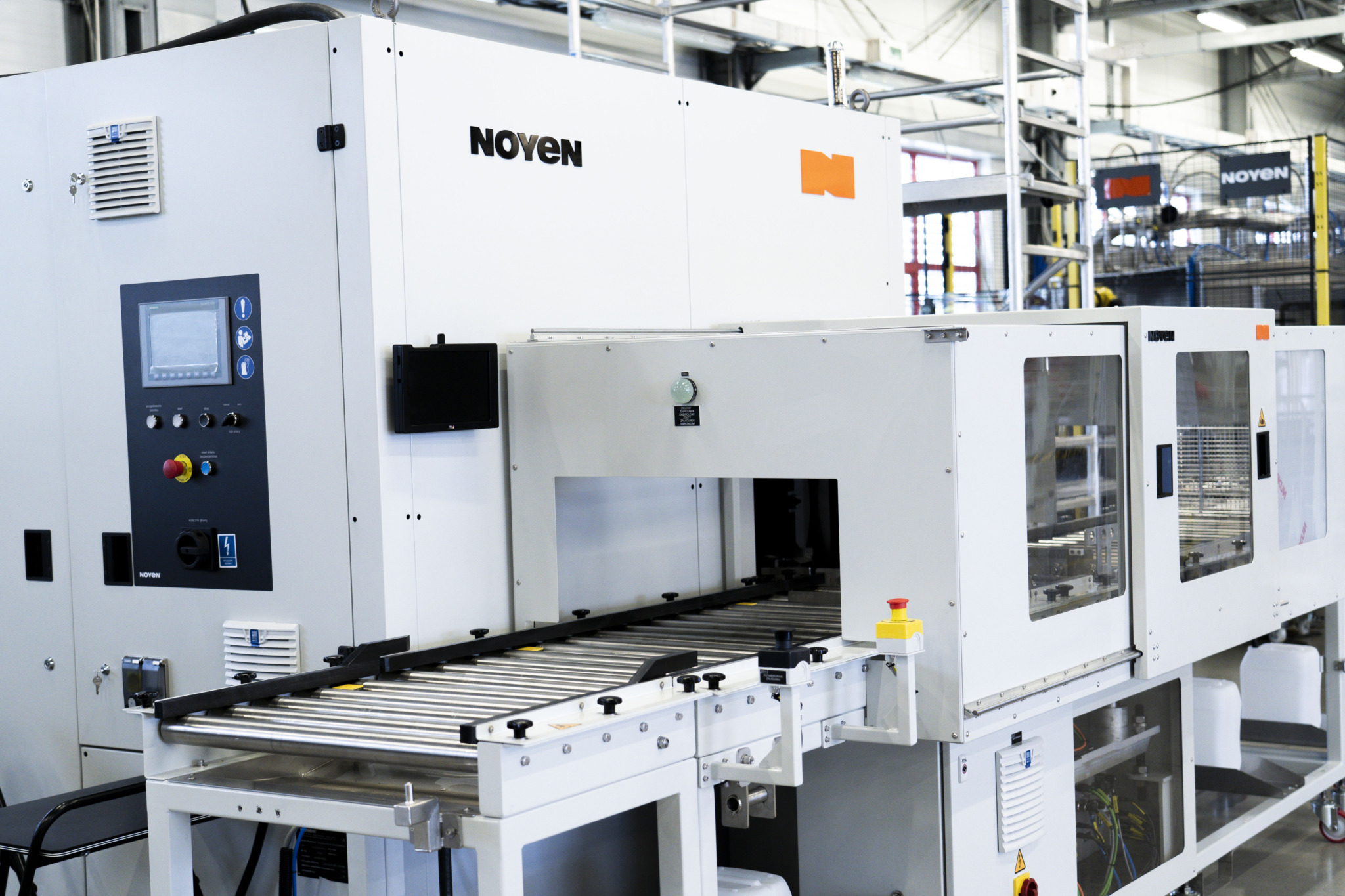
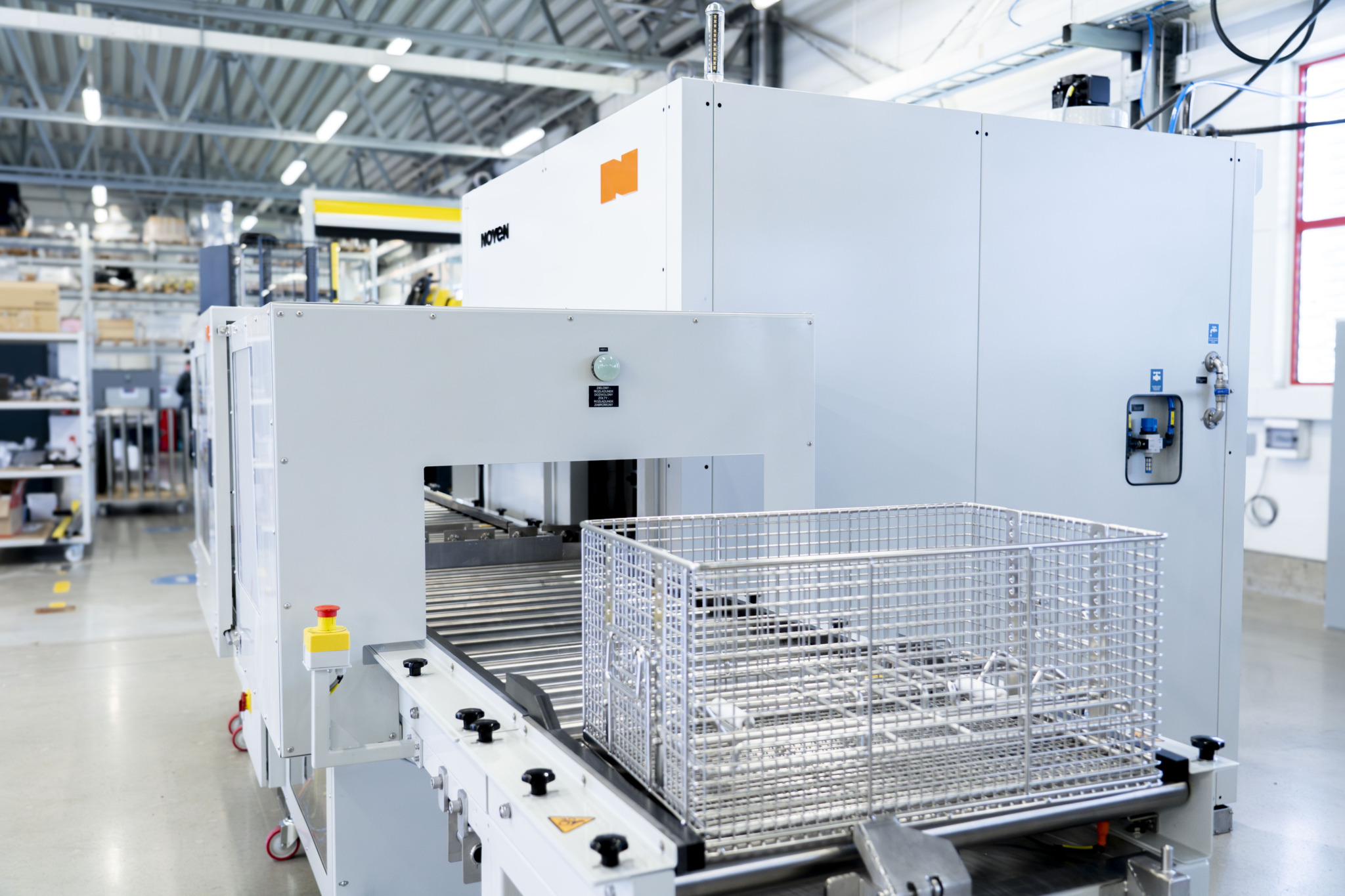
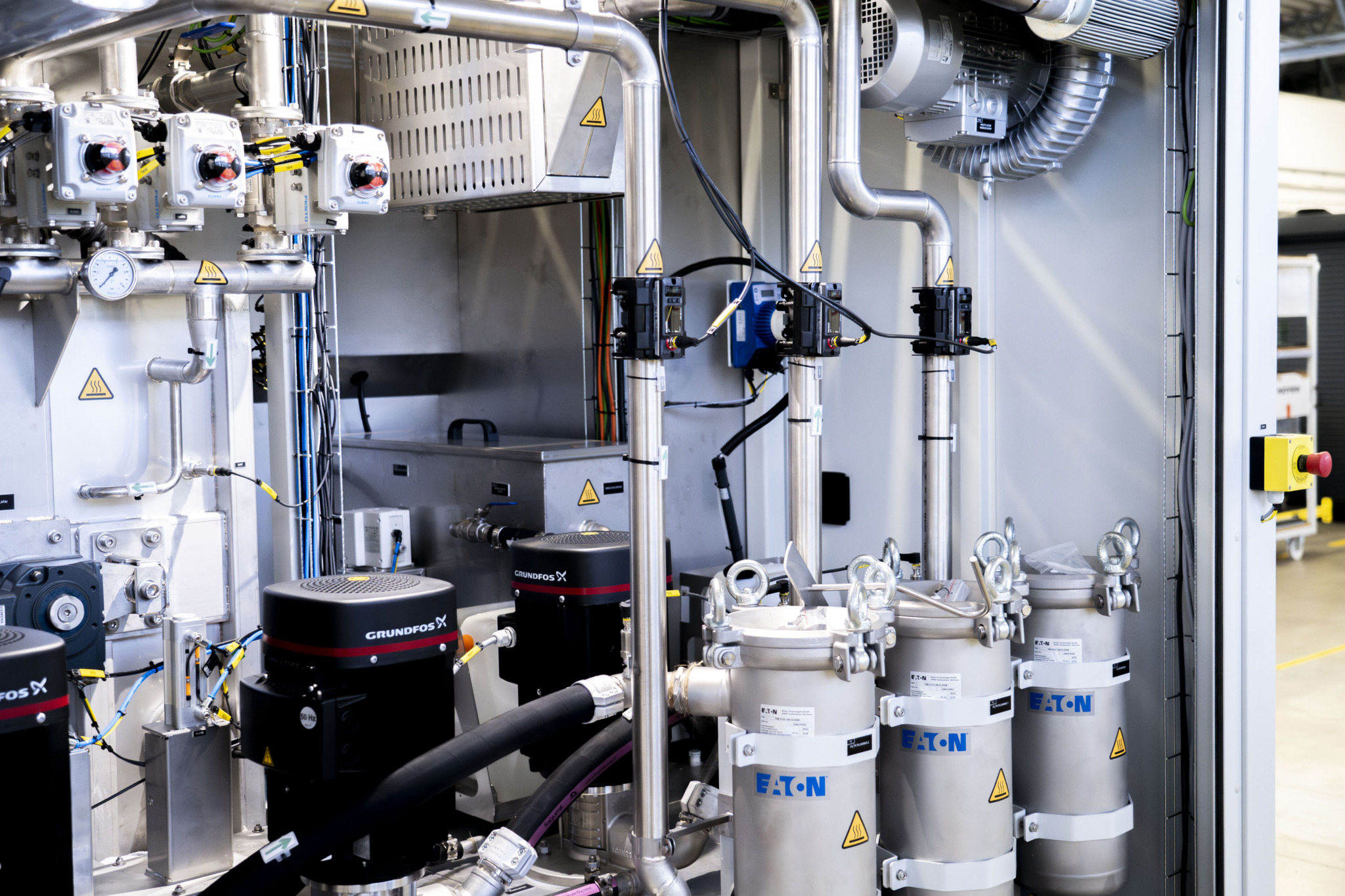
Nothing is impossible
It will be much easier if you tell us what is the matter. Save some time and sign up for a free consultation. Our expert will advise you free of charge.