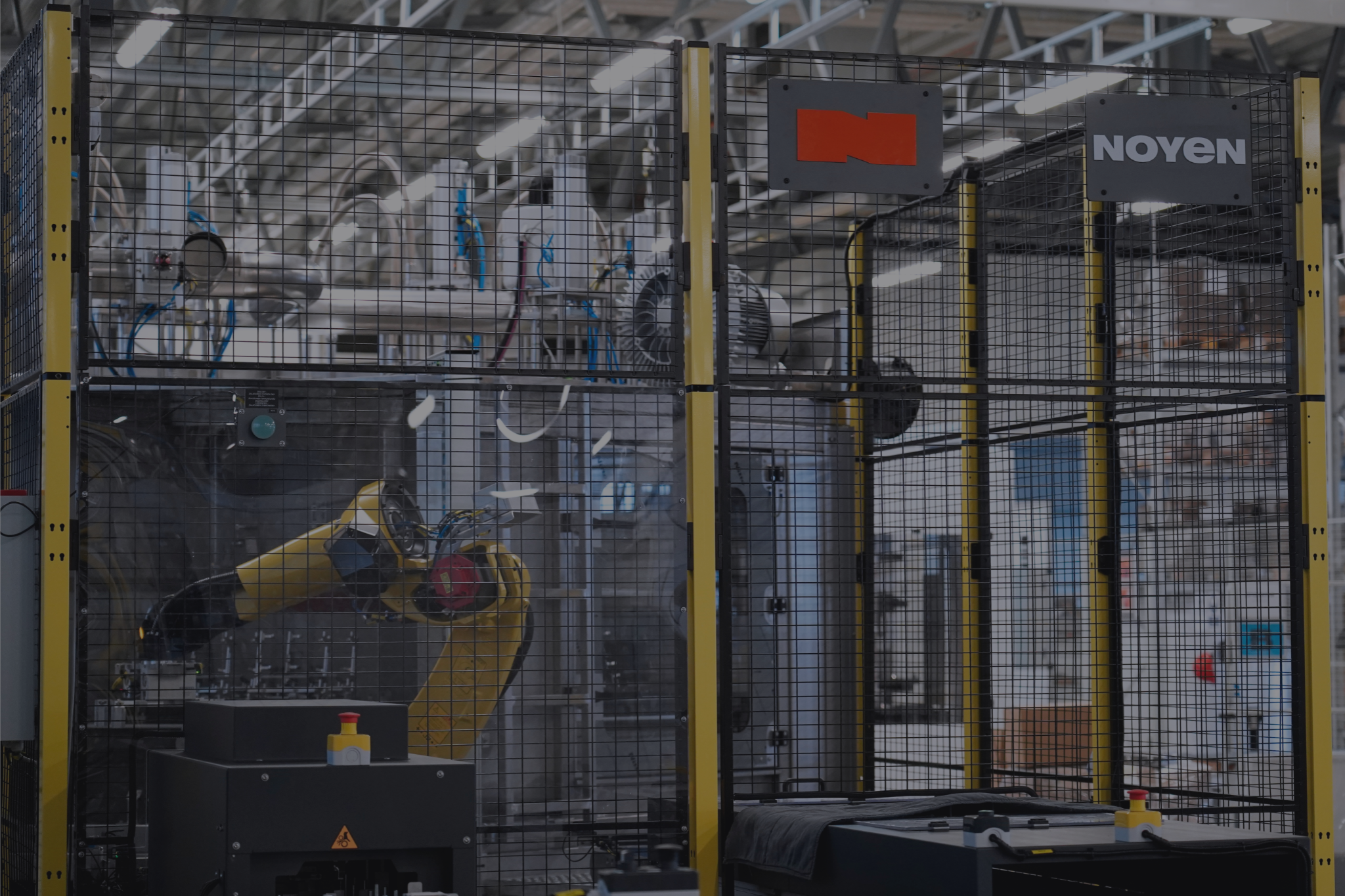
Our regular customer specializes in aluminum High Pressure Die Casting (HPDC) and supplies its products mainly to the automotive and electronics industries. Since 2017, when our cooperation began, we have equipped the customer’s machinery park with 6 washing machines.
What did the client need?
After the machining and finishing processes for castings, there was a need to clean the components of aluminum shot, metallic and non-metallic particles. The customer required both high process efficiency and high level of cleanliness of the parts destined for assembly.
The technical assumptions:
- Metallic and hard particles: max. 250 μm
- Non-metallic particles: max. 600 μm
- Surface tension level of the elements intended for bonding: 38 mN/m
- Cycle time: 35 seconds / part
- Capacity (annual requirement): 347,000 pcs.
Solution implemented at the customer’s site
We delivered the NOYEN Expert C carousel cleaning machine from the iCleaning Machine series. The ergonomic design provides easy access to key components, such as rotary indexing table, bath filters housings and tanks, which enables quick service and maintenance. The device has been designed for maximum reduction of energy consumption, which we have achieved e.g. through optimal dimensions of the washing chamber, effective thermal insulation and the use of dedicated filters. The project included the ability to wash two types of the covers without retooling.
- Dimensions of washing system with automation (mm): approx. 5000 (L) x 3200 (W) x 3000 (H)
- Process load: 4 x 1.5 kg
On the rotary table in one socket the machine can hold 4 parts. Robot with dedicated double gripper that separates clean and dirty workpieces has been installed for loading and unloading the parts. The work chamber is divided into five zones and the cleaning process includes the following stages: washing, double-stage rinsing, hot-air drying and vacuum drying. The machine has been equipped with blow off system between the mentioned sections, which prevents cross-contamination and bath transfer between tanks. Washing and rinsing of parts is carried out using spray manifolds with dynamic directional nozzles. Both sections have a dedicated fine filtration system to achieve the intended quality requirements.
The device is equipped with the iCleaning function – an innovative system for automatic sampling of bath contaminants in the form of a filter membrane for microscopic examination directly before the collector, which shows the actual condition of the liquid going onto the parts to be cleaned. This solution has significantly improved the ongoing control of contamination levels in the washing medium, while reducing laboratory operations and minimizing the risk of re-contamination.
In addition, the machine has a self-diagnostic function that allows checking the condition of the machine’s components and replacing damaged parts just in time. Performing the self-diagnostic procedure on a regular basis helps to predict potential machine malfunctions and maintain the machine’s optimum technical condition and process parameters.
Through the selection of the cleaning technology in the NOYEN laboratory we implemented NOYEN NP6 – a low-foaming concentrate, which is a special mixture that effectively removes oil contaminants and separates post-production and operational contamination from aluminum surface. It works at low concentrations and low temperatures, which saves electricity and process costs. This product ensured high cleaning process efficiency and achievement of the intended level of surface wettability. We also conducted a peel adhesion tape test on a washed surface, which result exceeded the assumed minimum in the customer’s specification three times.
Our collaboration with this customer is a perfect example of NOYEN’s comprehensive approach to industrial cleaning. In addition to delivering the equipment to the plant, we support the entire process – auditing the cleanliness of the production area and monitoring the level of contamination on the parts during storage, packaging and shipping to the end customer.
What does our client say about this project?
- We are a Tier 1 supplier and our end client is satisfied with the contract, because the efficiency and quality requirements of the washing process have been achieved.
- Loading and unloading have been automated, which has enabled the redirection of human resources to other needed areas.
- We have the ability to control the condition of the washing bath using the iCleaning function, which has made it easier for us to control the process and maintain it in stable parameters.
- We have the ability to minimize machine downtimes by regularly performing the self-diagnostic procedure, thanks to which our OEE has increased
- We have received full technological selection and constant support from NOYEN in the production process, which allows us to generate more profit and acquire further projects from the market with technical cleanliness.
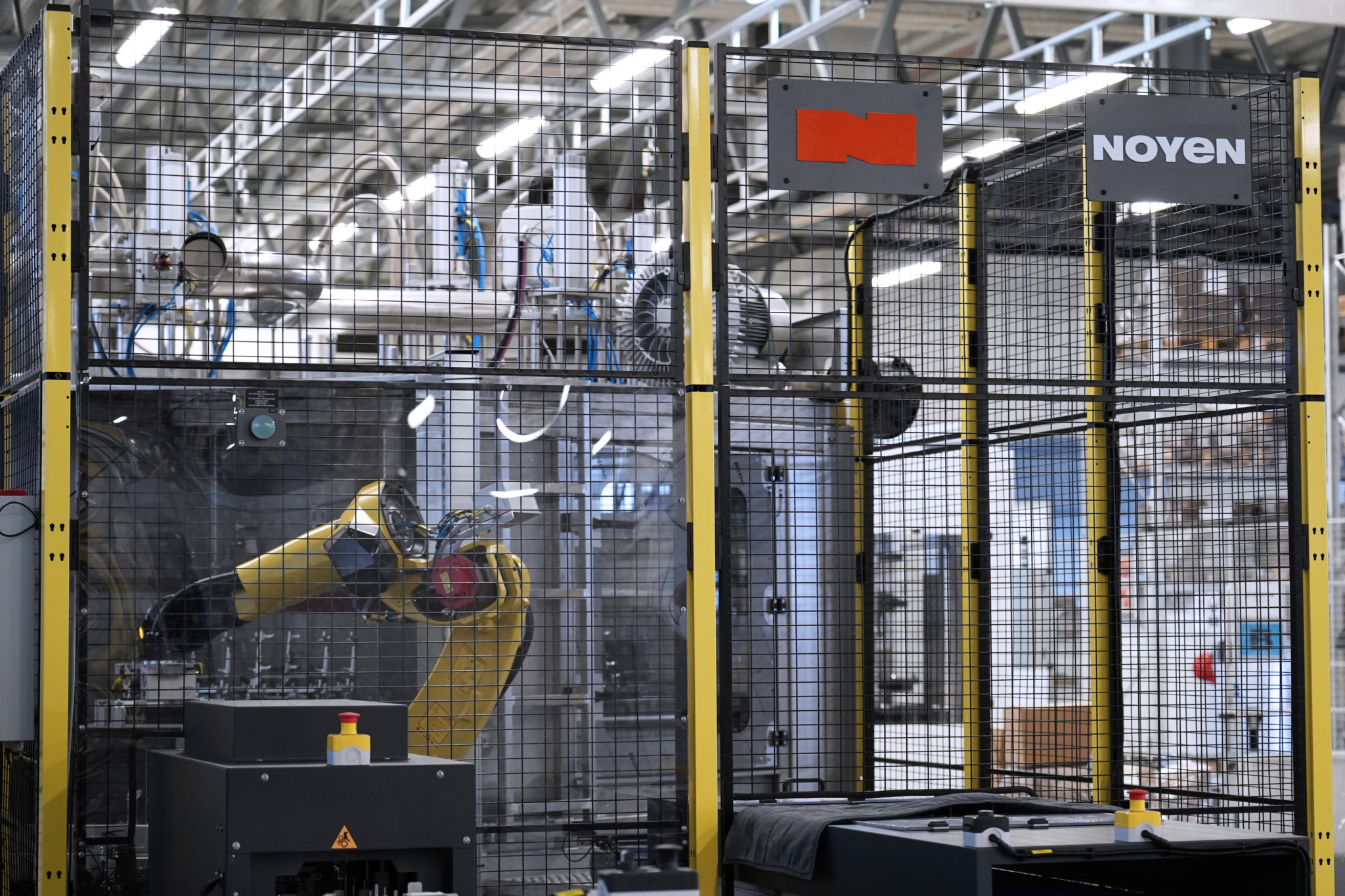
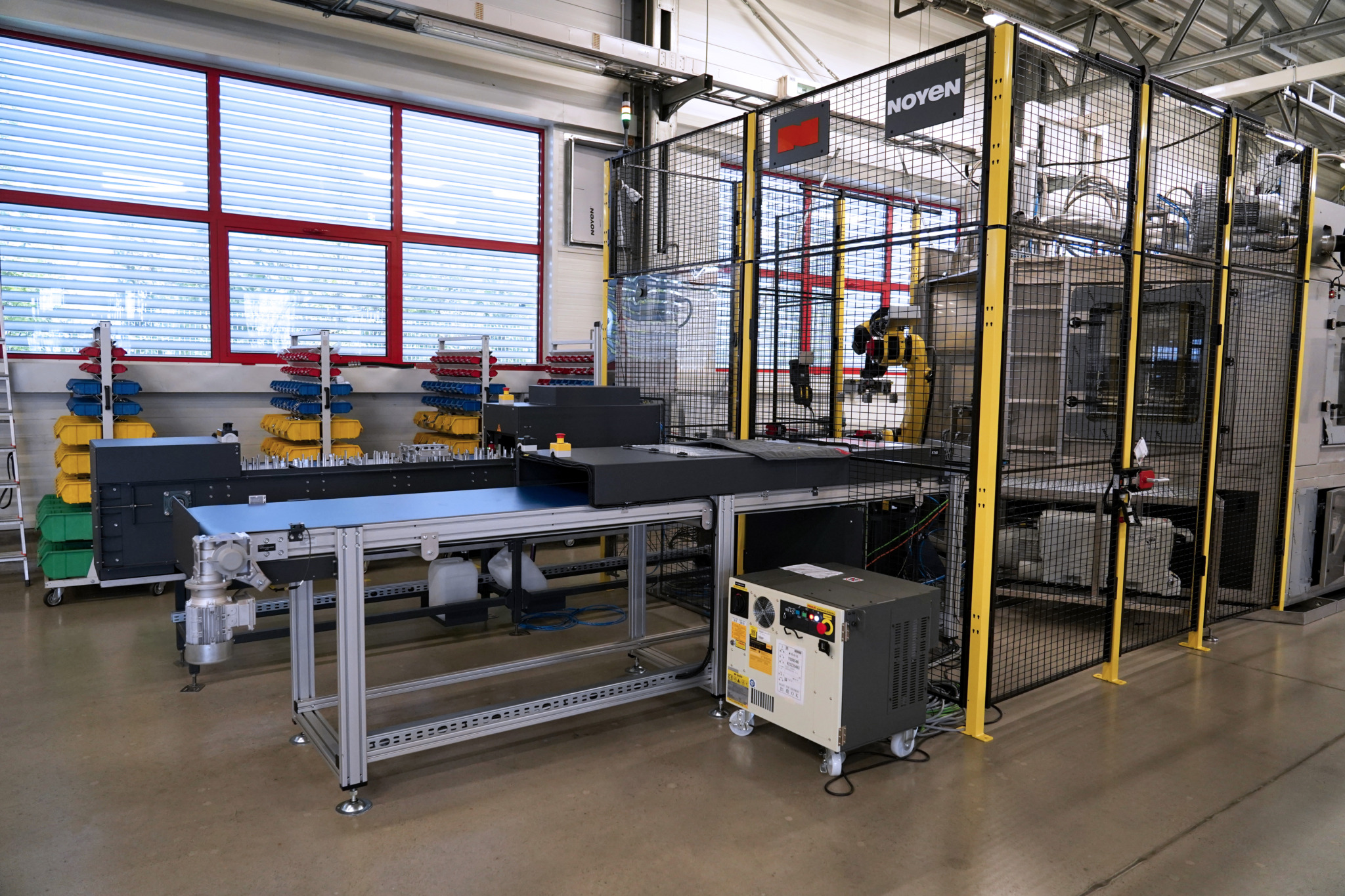
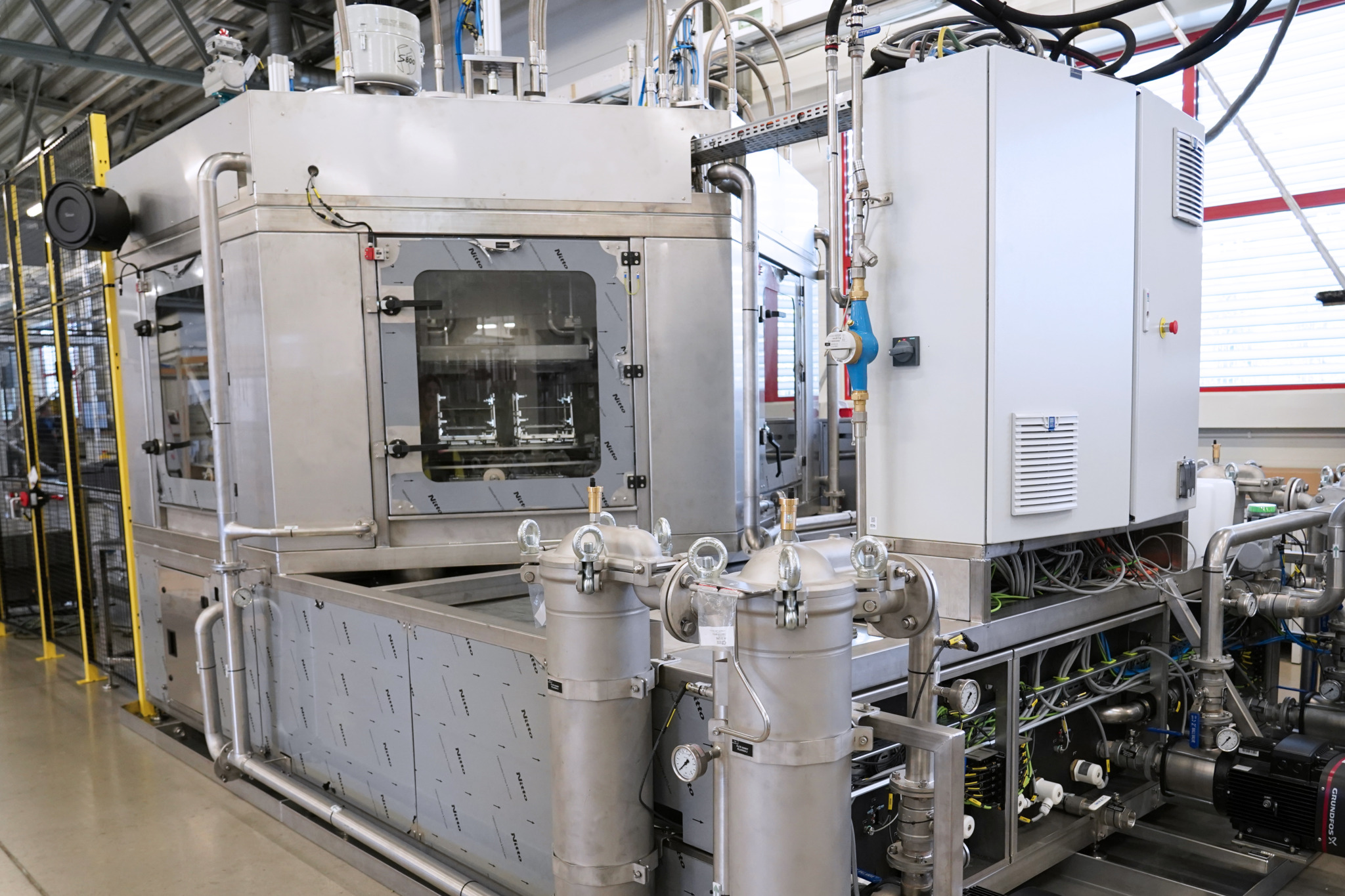
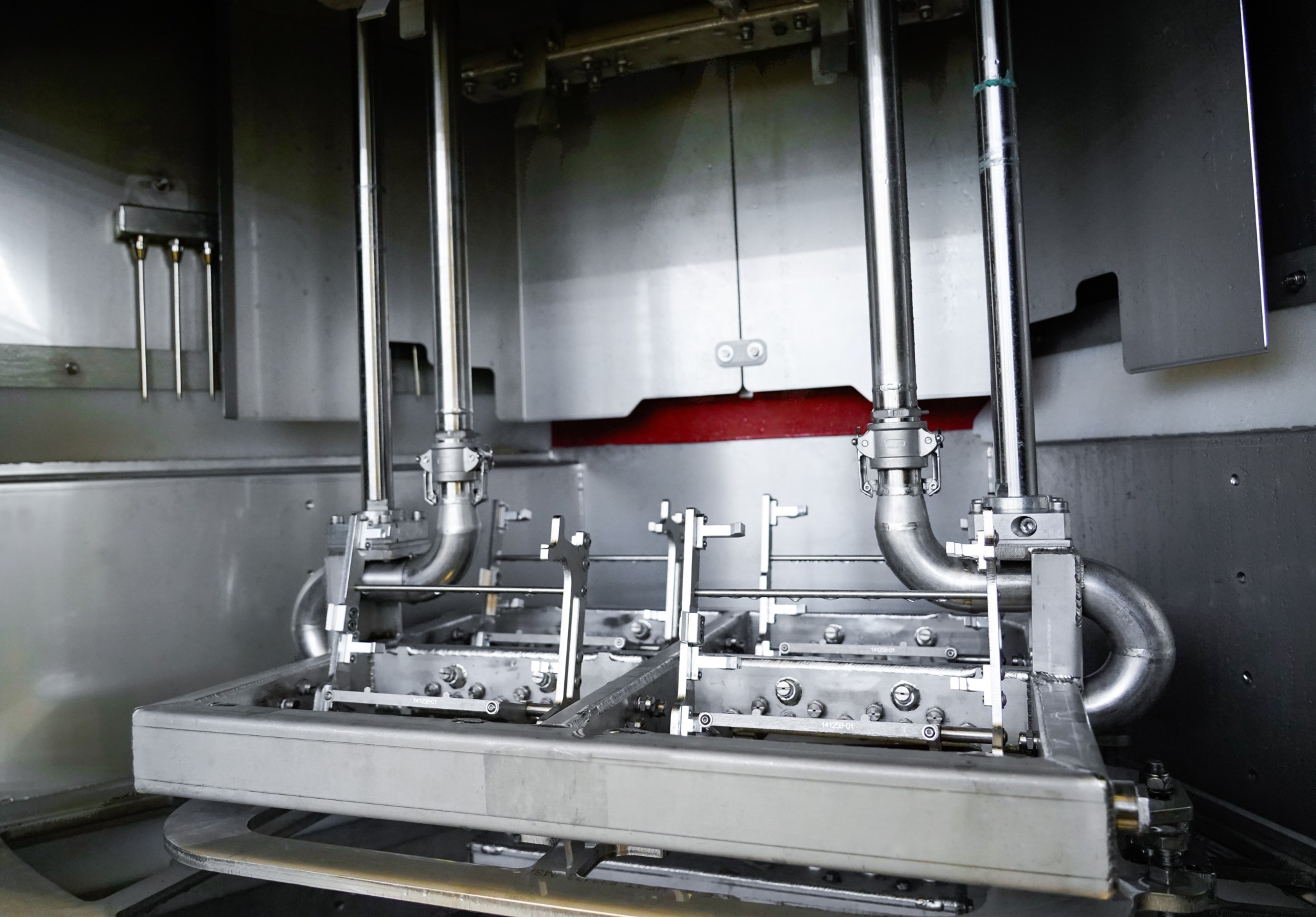
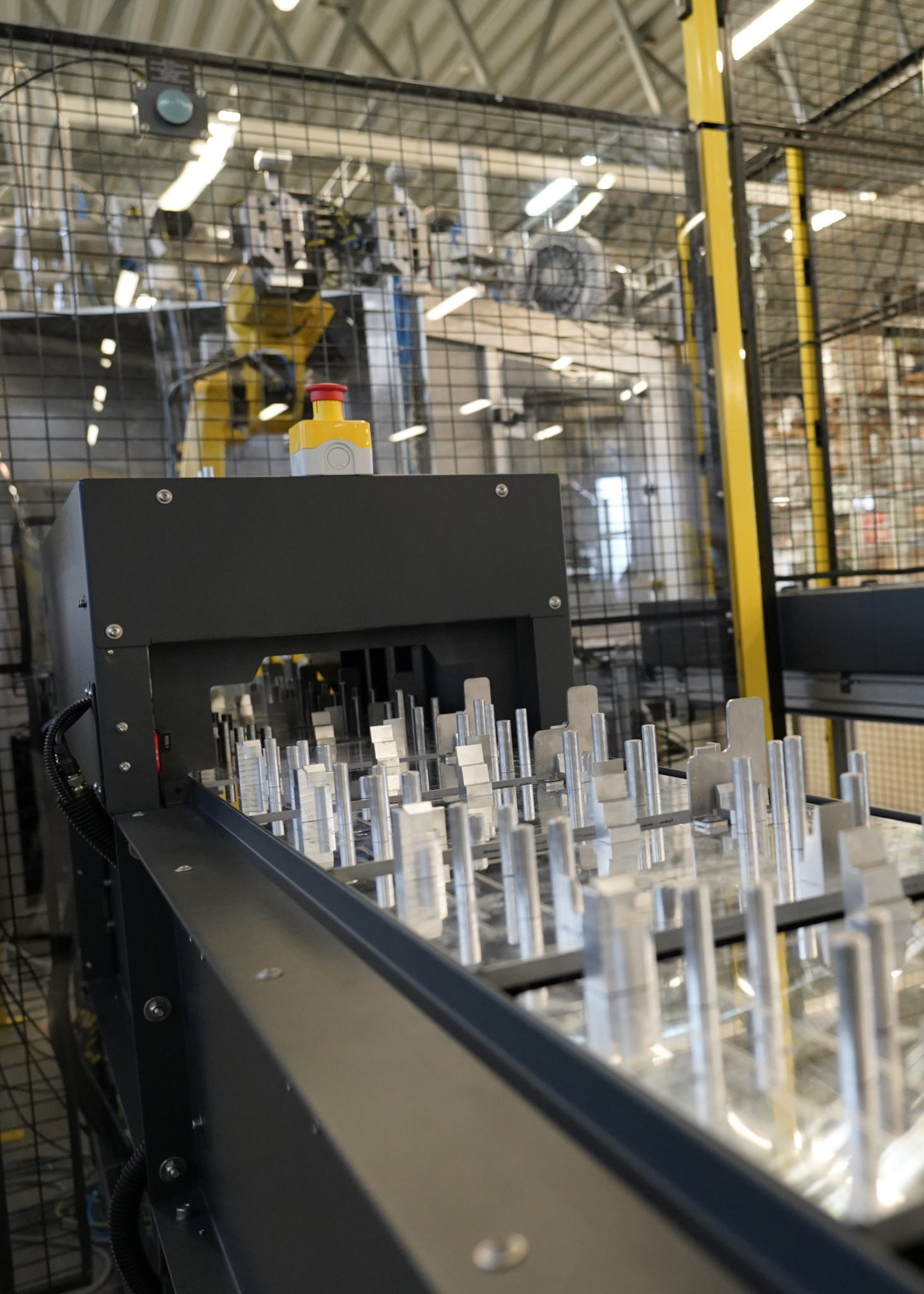
Nothing is impossible
It will be much easier if you tell us what is the matter. Save some time and sign up for a free consultation. Our expert will advise you free of charge.